flare9x
Petroleum
- Aug 30, 2018
- 24
In calculating the radius, R1:
Long radius = 1.5 * Pipe Diameter
Is the diameter the outside diameter OR the values taken from ASME B16.9 which are the inside diameter.... or the stated nominal pipe size.
Which diameter is used?
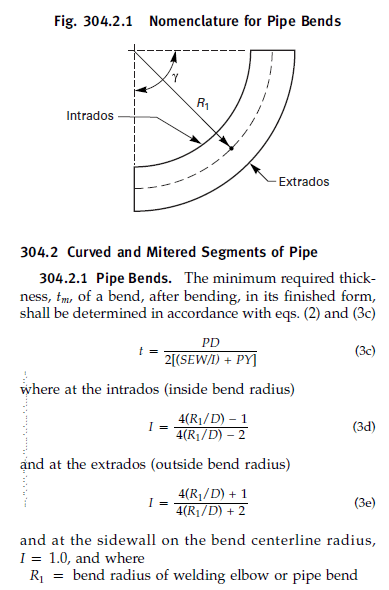
Long radius = 1.5 * Pipe Diameter
Is the diameter the outside diameter OR the values taken from ASME B16.9 which are the inside diameter.... or the stated nominal pipe size.
Which diameter is used?