Hi,
Our software has the following input screen for the calculation according to Appendix O-4 (Joint component approach) Ed. 2022:
The data entered refer to SA 193 B7 bolts, and a GMGC (Grooved Metal Flexible Graphite Covered) gasket according to API 660 Table 3:
According to API 660 7.8.2: "The minimum permissible bolt stress, Sbmin, and the maximum permissible bolt stress, Sbmax, shall be 40 %
and 70 %, respectively, of the listed yield values in the pressure design code at assembly conditions (i.e. ambient temperature)."; SA 193 B7 has a yield of 724 MPa at ambient, so respectively 289.6 and 506.8 MPa.
My doubt concerns the entry 'Flange damage', corresponding to 'Sfmax' on page 67 of ASME PCC-1:2022 (maximum permissible bolt stress prior to flange damage).
Still in the PCC, on page 74 Table O-4.1-2 there are Sfmax values referring to standard flanges in SA 105 (using elastic-plastic FEA).
Could you explain to me a way to find the correct Sfmax value to enter, especially for body flanges of heat exchangers, also by formulas, without the need for FEA?
I doubt that it is necessary to perform an FEA every time a flange joint of a heat exchanger is to be designed, for every flange when Appendix O-4 is required.
Thanks in advance
Our software has the following input screen for the calculation according to Appendix O-4 (Joint component approach) Ed. 2022:
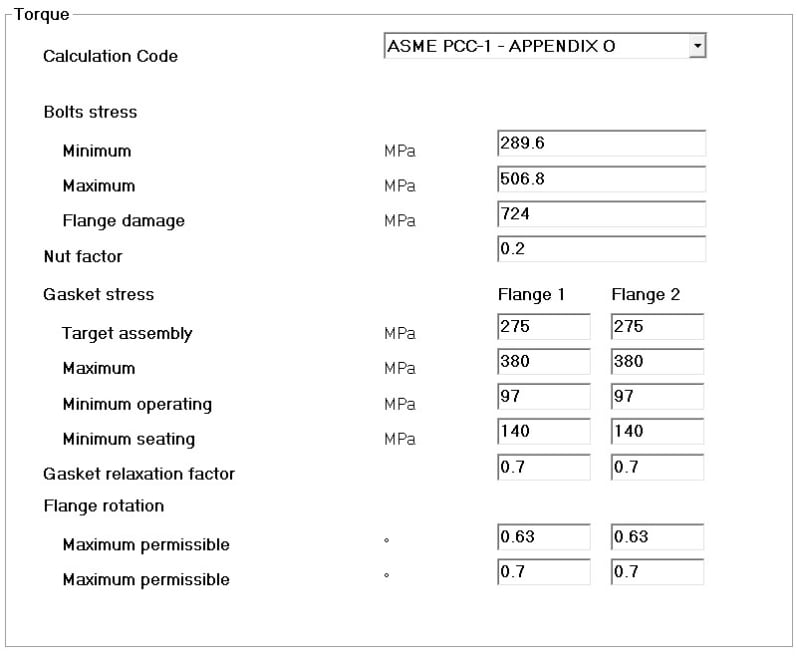
The data entered refer to SA 193 B7 bolts, and a GMGC (Grooved Metal Flexible Graphite Covered) gasket according to API 660 Table 3:
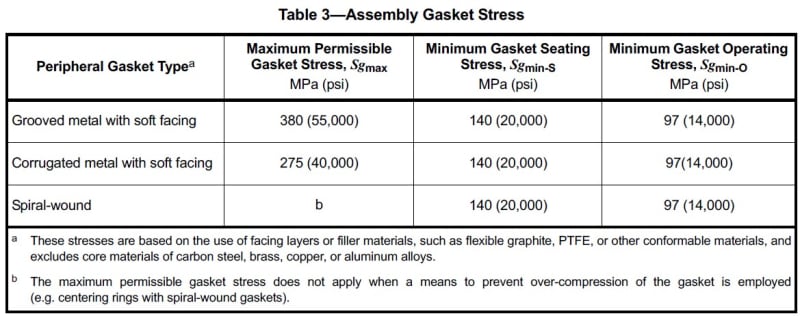
According to API 660 7.8.2: "The minimum permissible bolt stress, Sbmin, and the maximum permissible bolt stress, Sbmax, shall be 40 %
and 70 %, respectively, of the listed yield values in the pressure design code at assembly conditions (i.e. ambient temperature)."; SA 193 B7 has a yield of 724 MPa at ambient, so respectively 289.6 and 506.8 MPa.
My doubt concerns the entry 'Flange damage', corresponding to 'Sfmax' on page 67 of ASME PCC-1:2022 (maximum permissible bolt stress prior to flange damage).
Still in the PCC, on page 74 Table O-4.1-2 there are Sfmax values referring to standard flanges in SA 105 (using elastic-plastic FEA).
Could you explain to me a way to find the correct Sfmax value to enter, especially for body flanges of heat exchangers, also by formulas, without the need for FEA?
I doubt that it is necessary to perform an FEA every time a flange joint of a heat exchanger is to be designed, for every flange when Appendix O-4 is required.
Thanks in advance