scheideler
Civil/Environmental
- Mar 18, 2016
- 6
Hello. I've browsed this forum for years but couldn't find any info on my current issue so I thought I'd post.
I'm part of a team designing a deep well pump set which is assigned to a certain bandwidth of water surface elevations, although the water will rarely be that low (emergency pumps). In order to keep the pumps ready, we will exercise them regularly. The pumps will be equipped with VFDs, but at the minimum turn-down speed they are nowhere near where the system curve is likely to be. I've got some curves attached.
I understand that a back pressure valve (or pressure sustaining valve) can allow operation of the pumps even when the water surface is quite high, but, because of limitations on the design, the pump intake and the valve have a difference in elevation of ~250-ft. The flow path with the valve is a bypass with smaller piping than the process flow, requiring reduced flow rate.
Here are my questions.
Does one of these valves essentially establish a flat system curve (ie, a setting of 300 ft (converted to psi) means 300 feet at all flows)?
Does the sustained pressure exist equally throughout the riser pipe, or is there a significant elevation gradient? In other words, if i know what head the pump needs to see, how do I translate this to the valve setting, far above the pump? I'd found that, in order to stay in a good operating range as shown in the attached curve, the pump needs to see about 200-ft of head. But if i subtract the elevation difference, that leaves a setting of -50 ft, which obviously seems ridiculous.
I'd considered just running through a partially-closed ball valve (we'll be burning head anyway, but not for sustained periods), but found that the cavitation would be severe; is this reasonable?
Thanks in advance for any tips.
I'm part of a team designing a deep well pump set which is assigned to a certain bandwidth of water surface elevations, although the water will rarely be that low (emergency pumps). In order to keep the pumps ready, we will exercise them regularly. The pumps will be equipped with VFDs, but at the minimum turn-down speed they are nowhere near where the system curve is likely to be. I've got some curves attached.
I understand that a back pressure valve (or pressure sustaining valve) can allow operation of the pumps even when the water surface is quite high, but, because of limitations on the design, the pump intake and the valve have a difference in elevation of ~250-ft. The flow path with the valve is a bypass with smaller piping than the process flow, requiring reduced flow rate.
Here are my questions.
Does one of these valves essentially establish a flat system curve (ie, a setting of 300 ft (converted to psi) means 300 feet at all flows)?
Does the sustained pressure exist equally throughout the riser pipe, or is there a significant elevation gradient? In other words, if i know what head the pump needs to see, how do I translate this to the valve setting, far above the pump? I'd found that, in order to stay in a good operating range as shown in the attached curve, the pump needs to see about 200-ft of head. But if i subtract the elevation difference, that leaves a setting of -50 ft, which obviously seems ridiculous.
I'd considered just running through a partially-closed ball valve (we'll be burning head anyway, but not for sustained periods), but found that the cavitation would be severe; is this reasonable?
Thanks in advance for any tips.
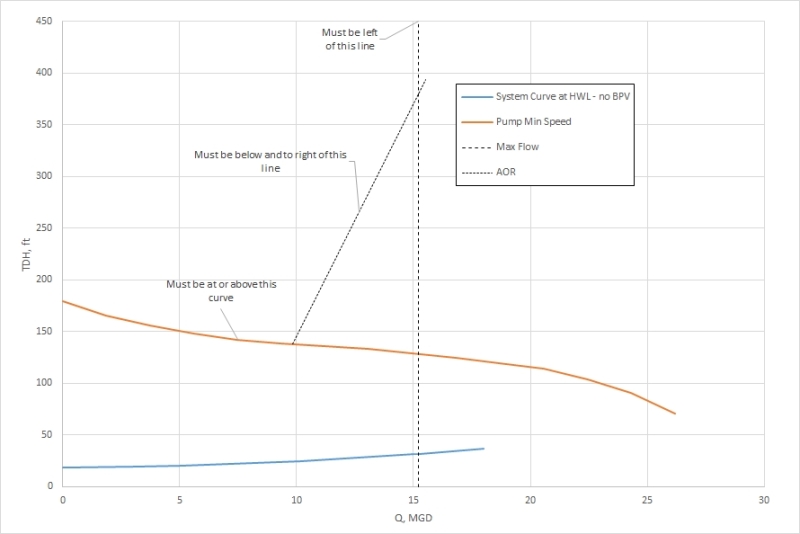