JohnRwals
Structural
- Jul 8, 2020
- 151
Hello!
I have a question related with barrier cable installation along the perimeter of parking structures.
These barrier cables are required for vehicle and pedestrian fall protection.
(My sketch does not show intermediate columns for the convenience.)
In my opinion, one continuous stand can be used with round plastic sleeves instead of four separate strands.
As I can use one strand, I can save many installation parts required wherever strands are cut off.
When I proposed this idea to some installation vendors, they did never install strands this way.
Can you think of any problem with this idea?
Thanks in advance!
JRW
I have a question related with barrier cable installation along the perimeter of parking structures.
These barrier cables are required for vehicle and pedestrian fall protection.
(My sketch does not show intermediate columns for the convenience.)
In my opinion, one continuous stand can be used with round plastic sleeves instead of four separate strands.
As I can use one strand, I can save many installation parts required wherever strands are cut off.
When I proposed this idea to some installation vendors, they did never install strands this way.
Can you think of any problem with this idea?
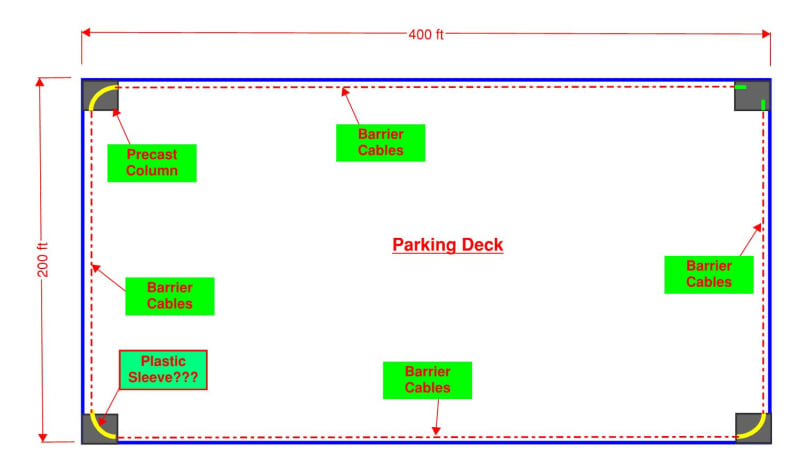
Thanks in advance!
JRW