CPBe
Structural
- Nov 4, 2019
- 17
Have an issue with a large piece of equipment sitting off the web of the main support beam - see sketch below:
Field crew claims the web is bending inward along with the top flange, and the member isn't even fully loaded yet.
What, in your opinion, would be the most economical approach to rectifying this issue?
Would, say, full-height stiffener plates along the beam's length (under the unit) make the most sense? Or maybe a channel member along the outside (accessible) portion of the beam?
Any advice/insight would be greatly appreciated.
Thank you in advance for your help!
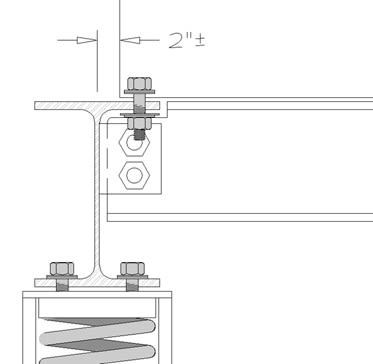
Field crew claims the web is bending inward along with the top flange, and the member isn't even fully loaded yet.
What, in your opinion, would be the most economical approach to rectifying this issue?
Would, say, full-height stiffener plates along the beam's length (under the unit) make the most sense? Or maybe a channel member along the outside (accessible) portion of the beam?
Any advice/insight would be greatly appreciated.
Thank you in advance for your help!