Abdelrahman_Yousef
Structural
- Jan 19, 2019
- 9
As the subjects suggests , this joint has been giving me headaches.
In the direction of the column main axis, I have a moment connected main beam and I need the back transverse stiffeners in the column.
How do I connect the strut and brace in the other direction while maintaining erect-ability of course .
I've seen the following 2 samples connections before, so can anyone give me advantages and disadvantages of each ?
what checks may be critical that might pass me by ?
or if there are any other suggested shapes.
In the direction of the column main axis, I have a moment connected main beam and I need the back transverse stiffeners in the column.
How do I connect the strut and brace in the other direction while maintaining erect-ability of course .
I've seen the following 2 samples connections before, so can anyone give me advantages and disadvantages of each ?
what checks may be critical that might pass me by ?
or if there are any other suggested shapes.
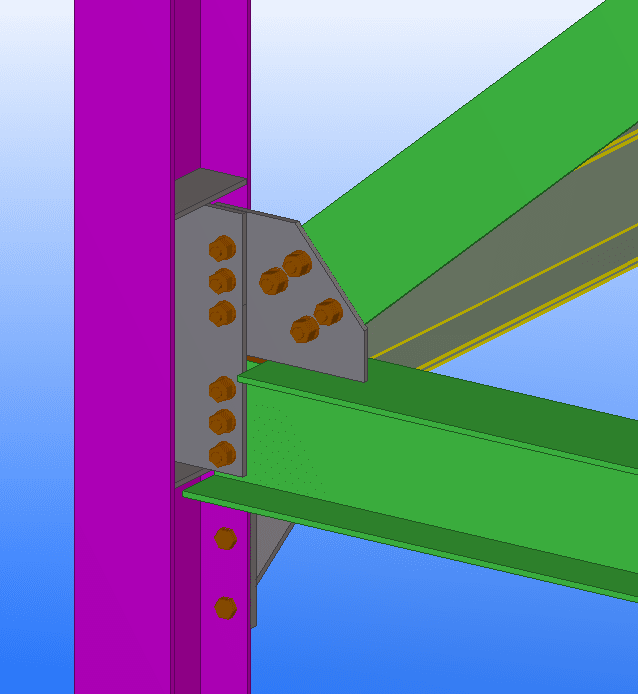
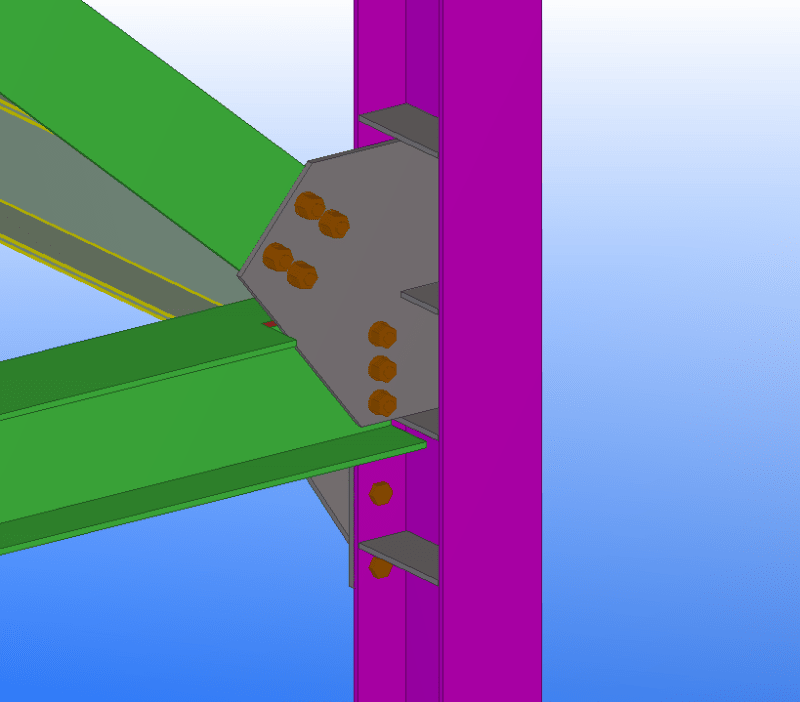