nguyen_v
Electrical
- Sep 4, 2024
- 3
Hello all,
I am currently designing a hollow shaft actuator using a custom compound planetary gearbox. The issue I am encountering is to find a way to couple the sun gear (15T, mod1) to the rotor, while still having the hollow shaft go through the sun gear. As the actuator is quite thin, the aun gear is limited in height (~12mm). I have seen a solution where some sort of custom gear coupler is machined to hold the sun gear.
Another solution that I've thought of is taking advantage of the radial exit of the gear cutter tool to get a larger base, where I can have room to add dowel pins for transmitting torque. However, this leaves a long section on the sun gear (highlighted in blue) where the planets cannot be engaged.
I feel like the first solution (machining a custom gear coupler, maybe having the sun and coupler with some profile shift) is currently the best way to go, but I've also seen designs with standard involute splines (something like ISO4156) directly embedded on the gear. In that case it would require sintered gears which is quite expensive for low volumes.
What are your thoughts?
I am currently designing a hollow shaft actuator using a custom compound planetary gearbox. The issue I am encountering is to find a way to couple the sun gear (15T, mod1) to the rotor, while still having the hollow shaft go through the sun gear. As the actuator is quite thin, the aun gear is limited in height (~12mm). I have seen a solution where some sort of custom gear coupler is machined to hold the sun gear.
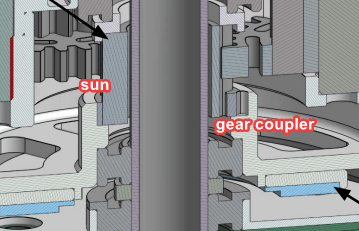
Another solution that I've thought of is taking advantage of the radial exit of the gear cutter tool to get a larger base, where I can have room to add dowel pins for transmitting torque. However, this leaves a long section on the sun gear (highlighted in blue) where the planets cannot be engaged.

I feel like the first solution (machining a custom gear coupler, maybe having the sun and coupler with some profile shift) is currently the best way to go, but I've also seen designs with standard involute splines (something like ISO4156) directly embedded on the gear. In that case it would require sintered gears which is quite expensive for low volumes.
What are your thoughts?