Hi dear sir ,
I work in Contractor.
I am responsible for Storage tanks.
We have one tank that keeps inside gas to liquid bio sludge in future.
We have performed hydrotest . But bottom plate went down , buckling came out .
Owner rejected it made Hyundai design company to revise drawing and to put channels all around the bottom.
my question is how this is serious that bio sludge product. Can the tank be safe with this product in near 30 years.
How to convince the Client that everything is ok.
I work in Contractor.
I am responsible for Storage tanks.
We have one tank that keeps inside gas to liquid bio sludge in future.
We have performed hydrotest . But bottom plate went down , buckling came out .
Owner rejected it made Hyundai design company to revise drawing and to put channels all around the bottom.
my question is how this is serious that bio sludge product. Can the tank be safe with this product in near 30 years.
How to convince the Client that everything is ok.
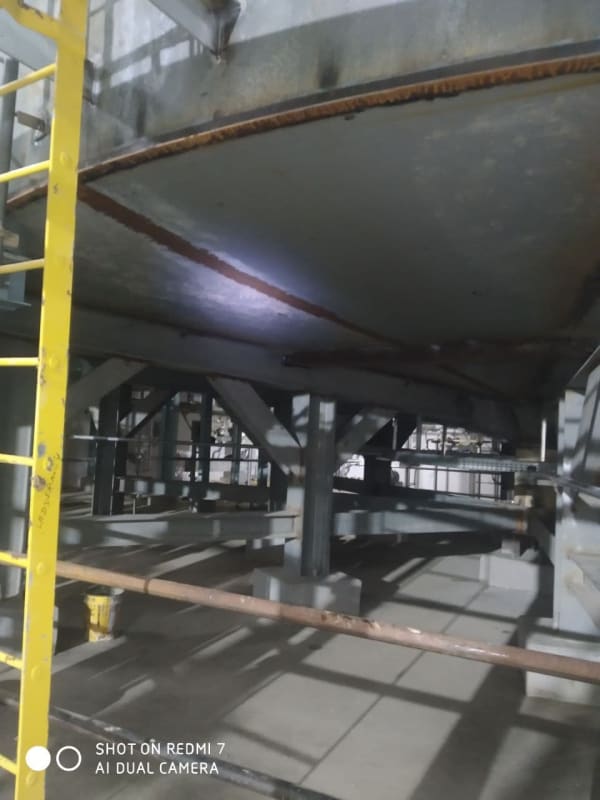