Mateus_R
Mechanical
- Mar 15, 2018
- 48
Hello everyone,
For a project I'm working, I have two flanges connected by bolts and I modeled the bolts as beam elements in ansys.
When I get the results from these beam elements, Ansys provided me 3 Forces and 3 Moments.
In this case, is it correct to transfer the bending moments coming from ansys as an additional axial force, or the axial force component already considers this effect?
This is not the case where I get a moment in the flange and I'm transferring to the bolts. These forces coming directly from the beam elements.
Thank you in advance.
For a project I'm working, I have two flanges connected by bolts and I modeled the bolts as beam elements in ansys.
When I get the results from these beam elements, Ansys provided me 3 Forces and 3 Moments.
In this case, is it correct to transfer the bending moments coming from ansys as an additional axial force, or the axial force component already considers this effect?
This is not the case where I get a moment in the flange and I'm transferring to the bolts. These forces coming directly from the beam elements.
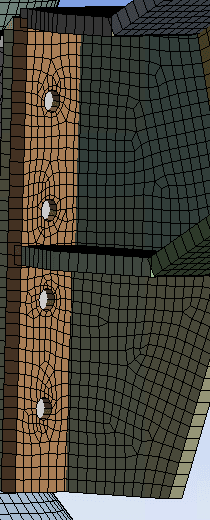
Thank you in advance.