Matt206
Mechanical
- Jan 21, 2019
- 9
Background:
A simple relatively accurate formula to relate Torque to Clamp Force is: T = (F)(D)(K).
Where D --= Diameter of bolt, T = Torque, Lets ignore K for this.
I am encountering a situation where a screw designed like #1 has an appropriate clamp force with the hand toque that we are able to generate. While a screw designed like #2 does not achieve the appropriate clamp force.
Thread type, thread engagement, material, is all exactly the same. As the above formula suggests, the diameter difference is the reason for the difference in holding force. I can actually feel the stretch that I am looking for when turning the smaller screw.
Question:My question is WHY does Diameter have an impact on this? I would think it would be cross sectional-area of the screw, But after drilling a through-hole in the larger diameter screw to decrease the cross sectional area (with the intention of making it function as a thinner spring to generate more stretch) this did not impact the clamp force.
If unable to change thread type, engagement, and diameter – I am unable to achieve the required clamping force with a given torque.
Picture 1:
Picture 2:
A simple relatively accurate formula to relate Torque to Clamp Force is: T = (F)(D)(K).
Where D --= Diameter of bolt, T = Torque, Lets ignore K for this.
I am encountering a situation where a screw designed like #1 has an appropriate clamp force with the hand toque that we are able to generate. While a screw designed like #2 does not achieve the appropriate clamp force.
Thread type, thread engagement, material, is all exactly the same. As the above formula suggests, the diameter difference is the reason for the difference in holding force. I can actually feel the stretch that I am looking for when turning the smaller screw.
Question:My question is WHY does Diameter have an impact on this? I would think it would be cross sectional-area of the screw, But after drilling a through-hole in the larger diameter screw to decrease the cross sectional area (with the intention of making it function as a thinner spring to generate more stretch) this did not impact the clamp force.
If unable to change thread type, engagement, and diameter – I am unable to achieve the required clamping force with a given torque.
Picture 1:
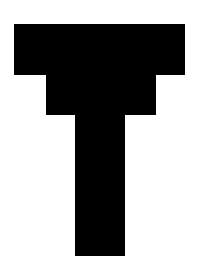
Picture 2:
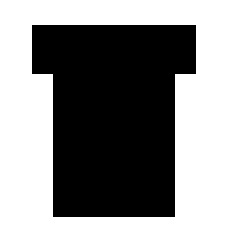