DJCoutts
Marine/Ocean
- Feb 25, 2016
- 14
Hi there
I'm currently trying to find a equation/formula to help show the applied for acting on a bolt and making sure its within the yield strength of the bolt.
From the image you have a davit with a load on the end, this will then transfers the force onto the bolts.
Currently i have used the shear formula and tensile to get the individual loading as followed
e.g.
Load : 6000N
Bolt : 10mm
Yield : 400MPa
Shear (single shear)
tress = Load / A..............A = 3.14 x 5^2 = 78.5398mm^2............6000 / 78.5389 = 76.3943N/mm^2 (MPa))
As there are 4 bolts holding it down then i devied the stress by the number of bolts for get the individual stress on each bolt..............76.3943 / 4 = 19.233575 MPa
400 / 19.233575 = 20.79 factor of safety (FoS)
Tensile (same formula as single shear)
Stress = Load / A..............A = 3.14 x 5^2 = 78.5398mm^2............6000 / 78.5389 = 76.3943N/mm^2 (MPa)
As there are 4 bolts holding it down then i devied the stress by the number of bolts for get the individual stress on each bolt..............76.3943 / 4 = 19.233575 MPa
400 / 19.233575 = 20.79 (FoS)
As the forces is not acting on the axis or in a shear formation but at 45Deg, do i need to have the force applied in each direct at 50%?
Also in not sure how to combine there's to get the overall stress on the bolt.
Im also aware that the load will course the davit to rotate in some wear between the base and end of the davit arm
If anyone can point me in the right direction it would be appreciated
I'm currently trying to find a equation/formula to help show the applied for acting on a bolt and making sure its within the yield strength of the bolt.
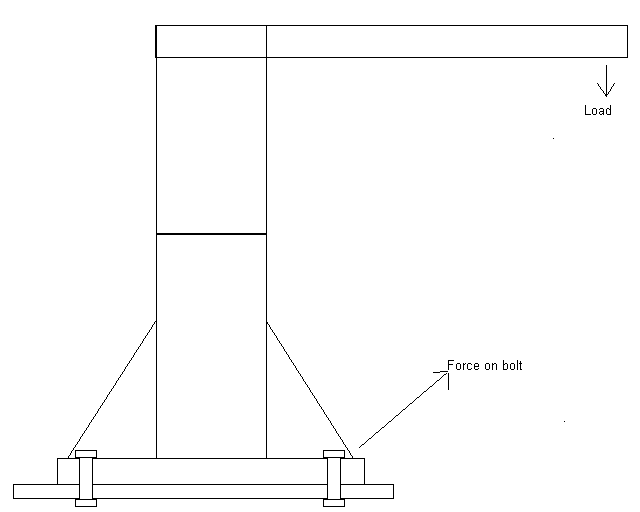
From the image you have a davit with a load on the end, this will then transfers the force onto the bolts.
Currently i have used the shear formula and tensile to get the individual loading as followed
e.g.
Load : 6000N
Bolt : 10mm
Yield : 400MPa
Shear (single shear)
tress = Load / A..............A = 3.14 x 5^2 = 78.5398mm^2............6000 / 78.5389 = 76.3943N/mm^2 (MPa))
As there are 4 bolts holding it down then i devied the stress by the number of bolts for get the individual stress on each bolt..............76.3943 / 4 = 19.233575 MPa
400 / 19.233575 = 20.79 factor of safety (FoS)
Tensile (same formula as single shear)
Stress = Load / A..............A = 3.14 x 5^2 = 78.5398mm^2............6000 / 78.5389 = 76.3943N/mm^2 (MPa)
As there are 4 bolts holding it down then i devied the stress by the number of bolts for get the individual stress on each bolt..............76.3943 / 4 = 19.233575 MPa
400 / 19.233575 = 20.79 (FoS)
As the forces is not acting on the axis or in a shear formation but at 45Deg, do i need to have the force applied in each direct at 50%?
Also in not sure how to combine there's to get the overall stress on the bolt.
Im also aware that the load will course the davit to rotate in some wear between the base and end of the davit arm
If anyone can point me in the right direction it would be appreciated