CardsFan1
Structural
- Mar 6, 2018
- 49
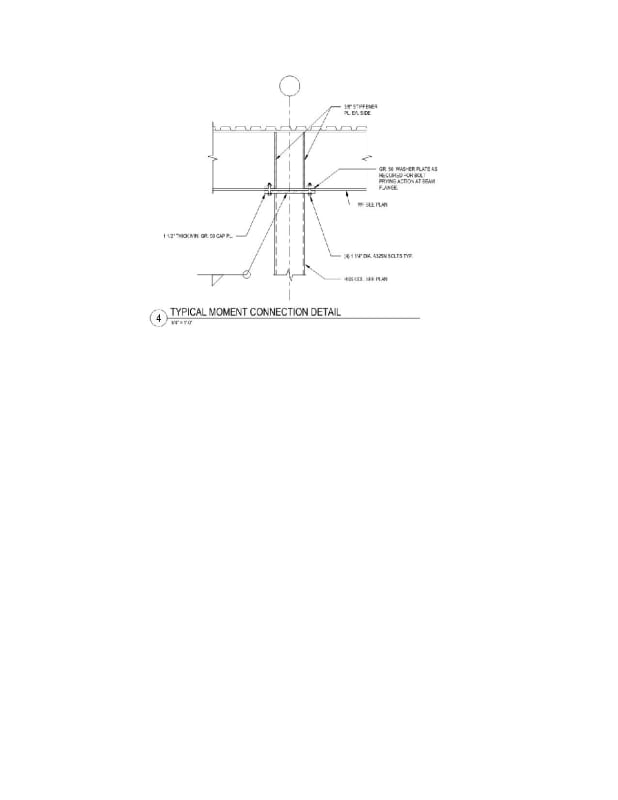
I am evaluating this connection and it has significant prying. The detail shows thick washers on the top side of the flange.
based on my understanding of prying, I don't see how this eliminates prying. If it does, how do you determine the thickness?
Does anyone have any experience with using thick washers to eliminate prying?