daparojo
Industrial
- Feb 25, 2010
- 36
Please could you review, and see if I am going along the correct lines.
I have a plate of 15 Bolts, and is subjected to Forces in the Fx, Fz and Fy plane. The forces can only act in one direction at anyone time. See attached diagram.
The undercut of the bolt (smallest area is 57mm)i.e. area,a = 2551mm2
The Bolt diameter in hole, D = 62mm, i.e. area A = 3019mm2
Number of Bolts, N = 15
By using the formula :- F For Shear Strength Of Material
------
A N
i.e. The worse case, Fx, the Shear Strength Needed For Bolt is 220 N/mm2
My Material has a Min. Yield of 650 N/mm2 UTS 820 N/mm2
Therefore, by Shear Strength of Material is 650 x 0.57 = 370 N/mm2 - Factor Of Safety of 1.4 (370N N/mm2/261 N/mm2)
The Tensile Required For The Bolt in Fy direction. a being the undercut, smallest area.
Fy
---------
a N
Tensile Stress in Bolt is 156 N/mm2 - So pretty low compared the Yield Of Material 650 N/mm2
But also, the Round Nut and Head Of Bolt will also help to hold the joint together in Fy direction.
Now I need to calculate the Load needed to help overcome the Forces.
Load = A x Shear Stress In Bolt (Fx - is the largest force)
Load = 667 kN Clamping Load Required (A Higher Initial Is Required To Stretch Bolt)
Total Load Across Plate = 665 kN x 15 = 10000 kN which seems ok as it obviously equals Fx
Now, would the bolts fail if the Loading was the same, yet the Fx force went up to say 13000 kN which is higher than the total Load ? Yet the Bolt Shear stress would go up to say to 287 N/mm2, but the clamp load remains the same, there will be less loading in the bolts then the force. Am I correct thinking that it won't fail due to the Shear Stress in Bolt/Material Shear Stress being well within limits?
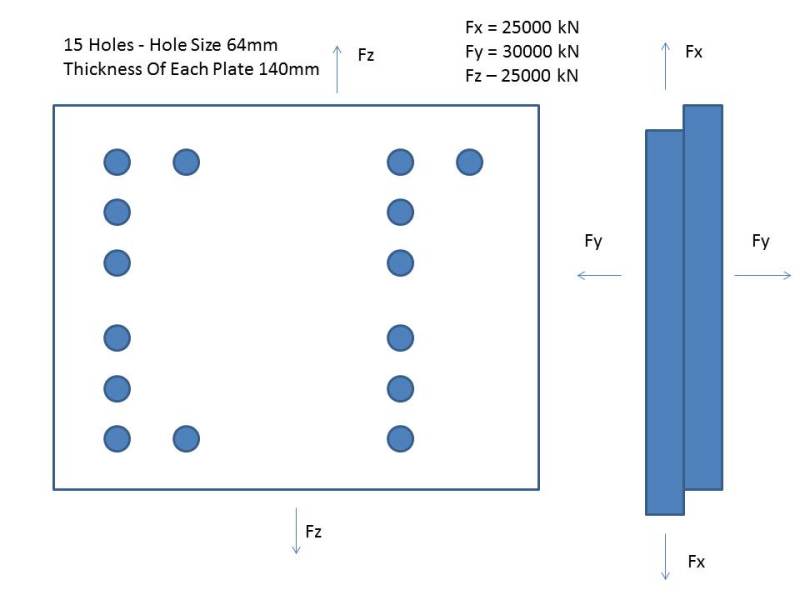
Many thanks