MatthewLynch
Mechanical
- May 27, 2024
- 10
Hello, I am trying to model a simply supported beam with a distributed load. The beam is formed with a C section channel and two plates that are welded, one on top and one on the bottom. To model this I am using NX and using CQUAD4 elements and have done a 1D connection Edge to Edge with RBE2 joining the plates to the C section channel.
Now I am trying to model the pin and roller for the simply supported beam. For this I have placed a point in the CG of the section at each end and I am connecting the point to the edges with RBE2 elements. The idea of this is to be able to allow it to rotate maintaining it flat.
Now when I analyze my results they do not look as I expect.
Here is an image of the stress on XX
For a simply supported beam I would expect compression on the top and tracction on the bottom, as seen in te center. But we can see that this does not happen at the supports. There I am getting traction on top and compression on the bottom. So it is not working as a simple supported beam.
If I look in detal the Z displacements of the edge I can see that the face of the beam rotates, but there is no displacement in Z. So I guess that it is expanding then?
I have placed it at the top to have a reference on hight and see that there is no displacement in Z direction.
What am I doing wrong? what would be the best way to model a simply supported beam? Do I have to release some of the DOF's on the RBE2? What DOF should I release in that case? I do not fully understand how the DOF releasing on RBE2 elements works.
Thank you
Now I am trying to model the pin and roller for the simply supported beam. For this I have placed a point in the CG of the section at each end and I am connecting the point to the edges with RBE2 elements. The idea of this is to be able to allow it to rotate maintaining it flat.
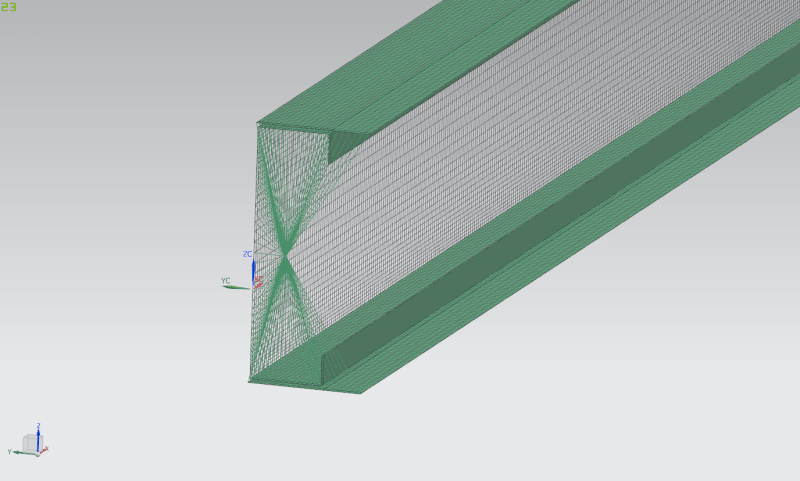
Now when I analyze my results they do not look as I expect.
Here is an image of the stress on XX
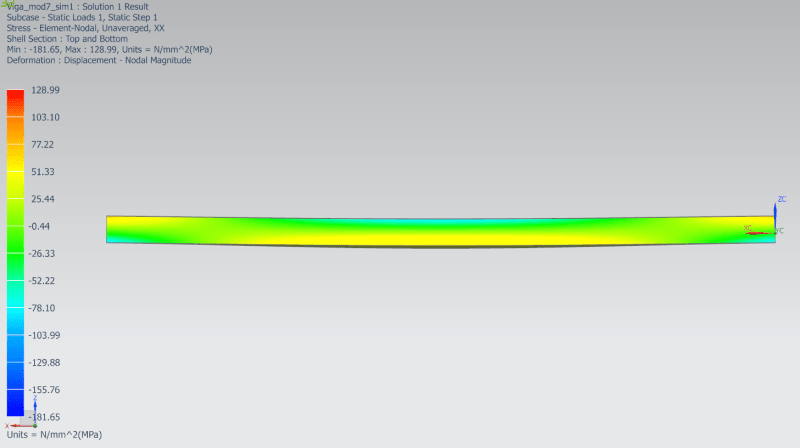
For a simply supported beam I would expect compression on the top and tracction on the bottom, as seen in te center. But we can see that this does not happen at the supports. There I am getting traction on top and compression on the bottom. So it is not working as a simple supported beam.
If I look in detal the Z displacements of the edge I can see that the face of the beam rotates, but there is no displacement in Z. So I guess that it is expanding then?
I have placed it at the top to have a reference on hight and see that there is no displacement in Z direction.
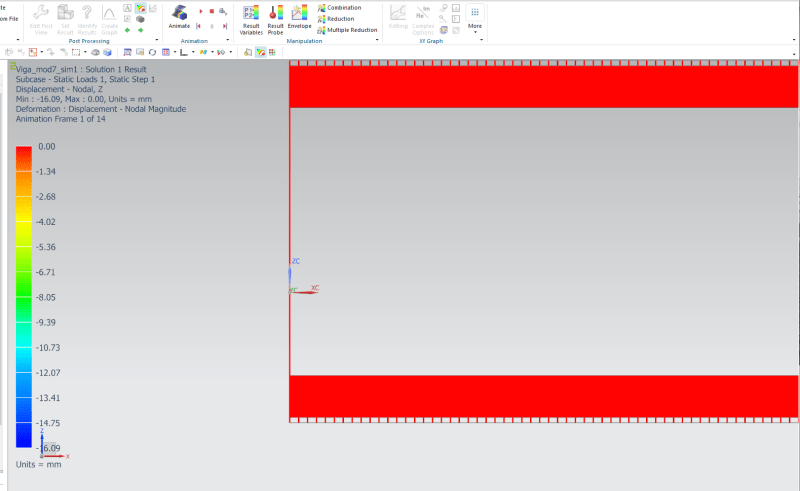
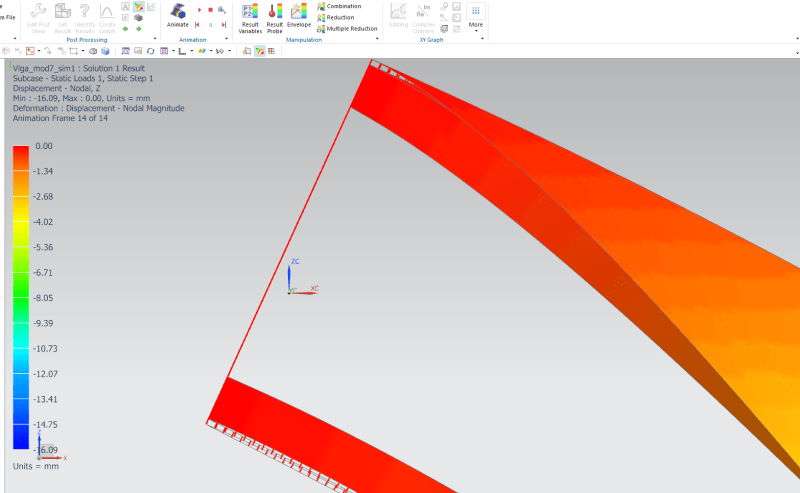
What am I doing wrong? what would be the best way to model a simply supported beam? Do I have to release some of the DOF's on the RBE2? What DOF should I release in that case? I do not fully understand how the DOF releasing on RBE2 elements works.
Thank you