PIPING_DESIGNER
Mechanical
- Feb 16, 2021
- 42
How to reduce stress on elbow of a buried GRE/GRP pipeline ?
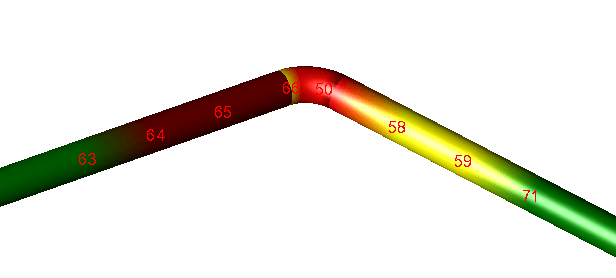
Follow along with the video below to see how to install our site as a web app on your home screen.
Note: This feature may not be available in some browsers.