smithtasticness
Industrial
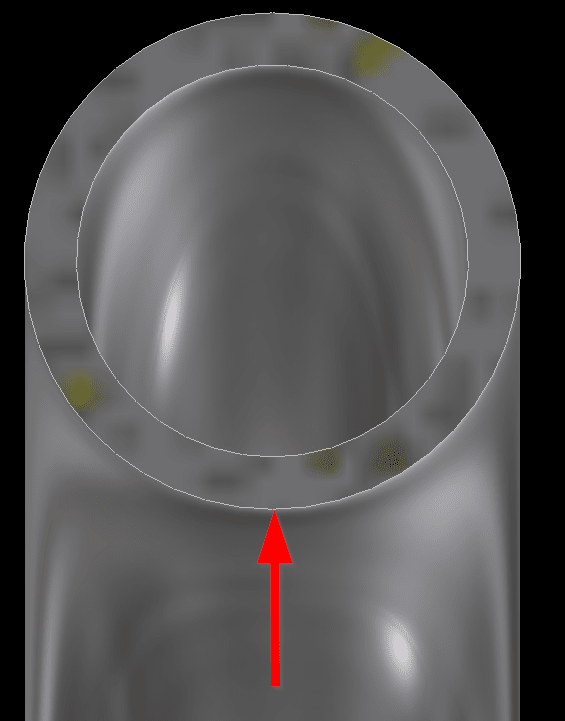
I have some tube (see above & ignore the fact that it's bent for now) and I'm trying to find out how I can calculate the force or load it'll take before the tube crushes.
I can't seem to find this anywhere but I think I might be looking in the wrong places. I've found plenty of buckling formula but I'm almost certain that those are either for compressive strength or for buckling along a given length. I think what I need is much simpler, but I'm totally lost on this one. I'm hoping someone here might be able to point me in the right direction.
I'm assuming that realistically I should only need the cross-section properties and material properties to be able to figure it out but at the moment I cannot see the light.
Thanks in advance.