marinovich.91
Marine/Ocean
Referencing the thread thread1083-462143
How to find max pressure of hydraulic cylnder which is actuateing the ships rudder if my rudder surface is as seen from picture.
Firstly,
I found on online calculator and tried to calculate the stalling drag for ruder at 35 degrees and it gave me that force of drag is 521N.
Can you tell me if I am doing something incorectly in my calculations...
In drag force calculator i used foloving:
Density of 1030 kg/m3 (seawater)
Area of 0.2 m2 since my rudder is balanced and one side cancels another
Drag coeficient of 0.6 since I found that hydrofoil has stall drag coeficient of 0.6 at 35°
6.5miles is cruiseing speed of my boat
A
Considering that this drag is made from 15-20cm(17.5cm approx) off the main shaft of rudder. It is makeing 521N x 0.175m = 91Nm of torque on shaft at maximum ruder angle.
On the other hand rudder is actuated with cylnder as on atached picture.
It is attached to rudder shaft over 15cm
Tiller arm.
By my calculation it would mean that force on cylnder is 606N at max obtainable rudder angle- what is actually max pressure possible to reach in system.
I need to find a way to calculate max pressure in order to corectly chose my cylnder as explained in topic before.
As seen in topic before, I would like to chose the cylnder for rudder in such way that I get 4kg/m at sterring pump shaft at max pressure in the system.
Thanks.
Please corrext me if I did mistakes a long the way
How to find max pressure of hydraulic cylnder which is actuateing the ships rudder if my rudder surface is as seen from picture.
Firstly,
I found on online calculator and tried to calculate the stalling drag for ruder at 35 degrees and it gave me that force of drag is 521N.
Can you tell me if I am doing something incorectly in my calculations...
In drag force calculator i used foloving:
Density of 1030 kg/m3 (seawater)
Area of 0.2 m2 since my rudder is balanced and one side cancels another
Drag coeficient of 0.6 since I found that hydrofoil has stall drag coeficient of 0.6 at 35°
6.5miles is cruiseing speed of my boat
A
Considering that this drag is made from 15-20cm(17.5cm approx) off the main shaft of rudder. It is makeing 521N x 0.175m = 91Nm of torque on shaft at maximum ruder angle.
On the other hand rudder is actuated with cylnder as on atached picture.
It is attached to rudder shaft over 15cm
Tiller arm.
By my calculation it would mean that force on cylnder is 606N at max obtainable rudder angle- what is actually max pressure possible to reach in system.
I need to find a way to calculate max pressure in order to corectly chose my cylnder as explained in topic before.
As seen in topic before, I would like to chose the cylnder for rudder in such way that I get 4kg/m at sterring pump shaft at max pressure in the system.
Thanks.
Please corrext me if I did mistakes a long the way
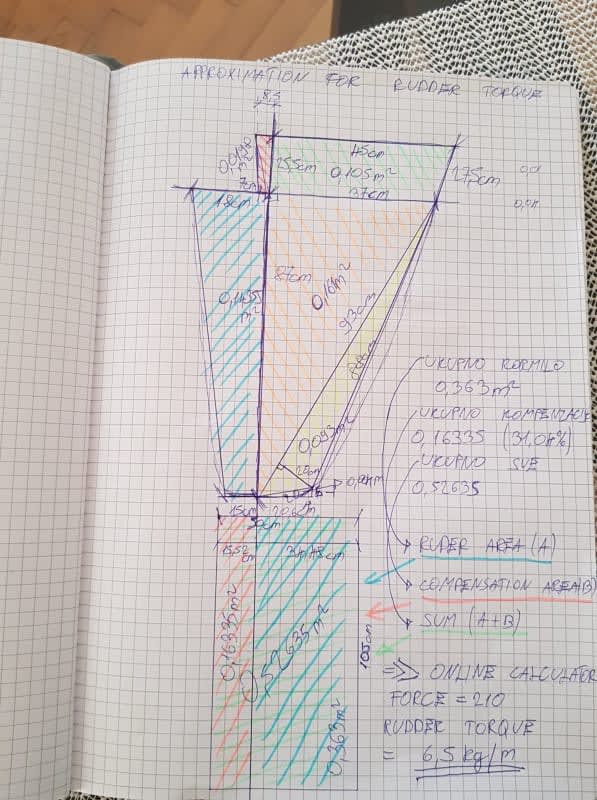
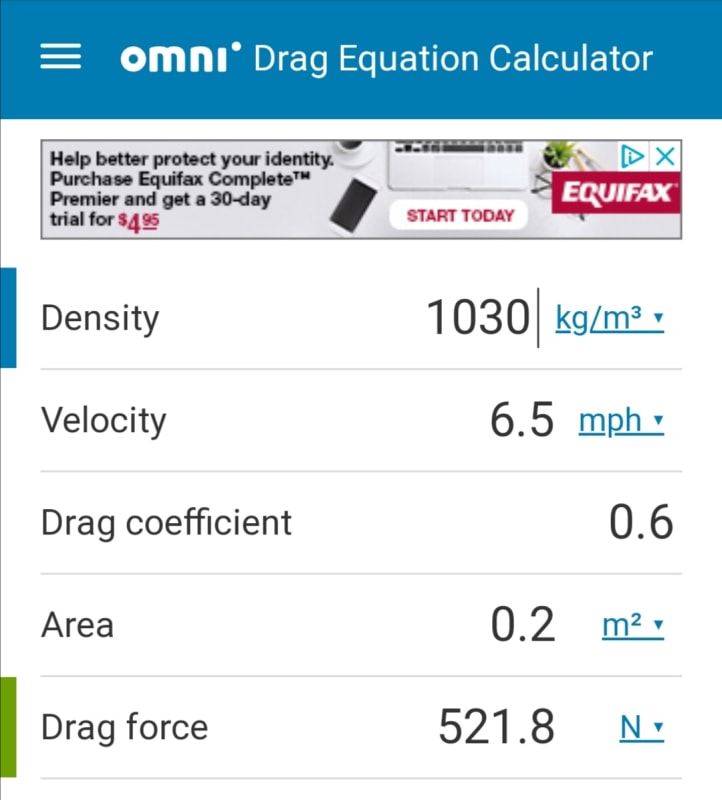
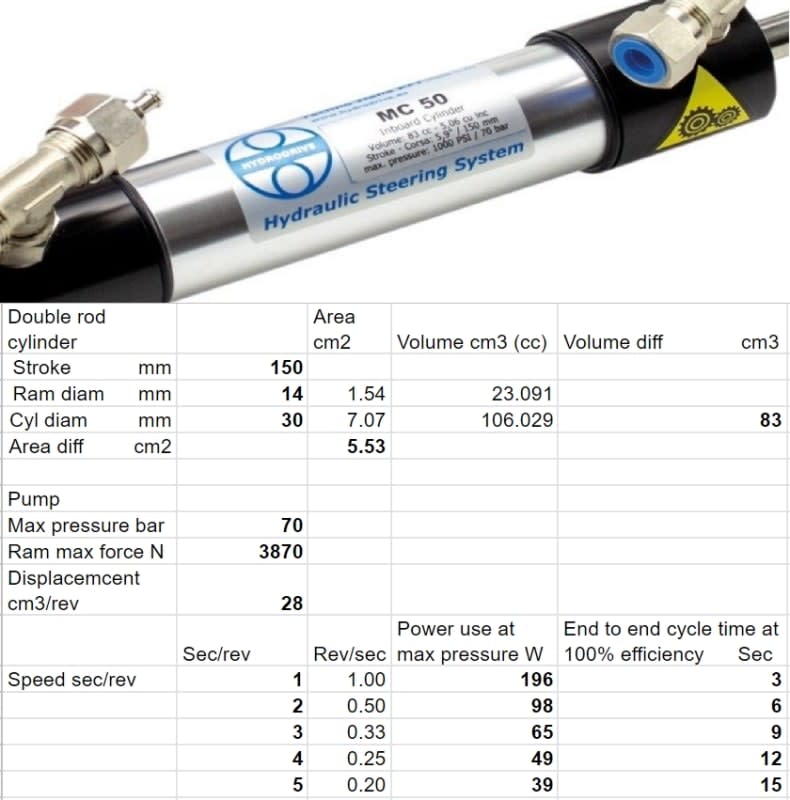