canstruct12
Structural
- Dec 18, 2018
- 26
Hi all, I am trying to calculate the shear area for a built-up section for input in STAAD.
I have found a number of resources to determine built-up section shear area, but have not bee able to find any guidance on calculation of the shear area for this specific configuration: W-Shape with a W-Shape cap.
For reference, the W-Shape with a W-Shape cap shape is used as leg of a bent which supports a truss carrying an open channel flume.
Thanks, CS12
I have found a number of resources to determine built-up section shear area, but have not bee able to find any guidance on calculation of the shear area for this specific configuration: W-Shape with a W-Shape cap.
For reference, the W-Shape with a W-Shape cap shape is used as leg of a bent which supports a truss carrying an open channel flume.
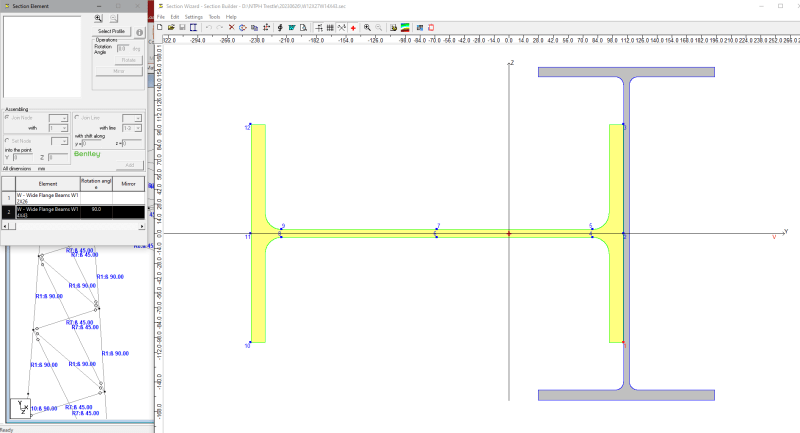
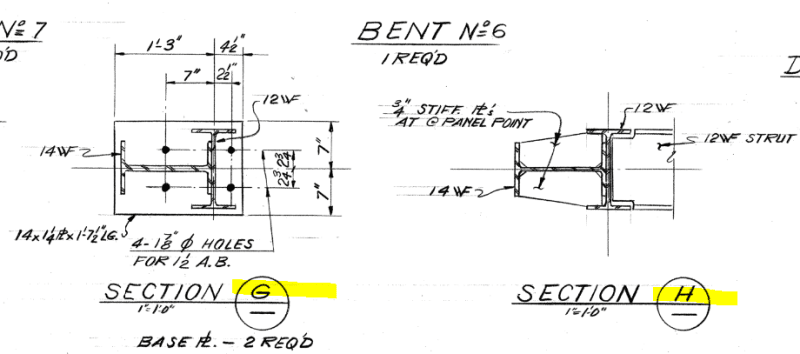
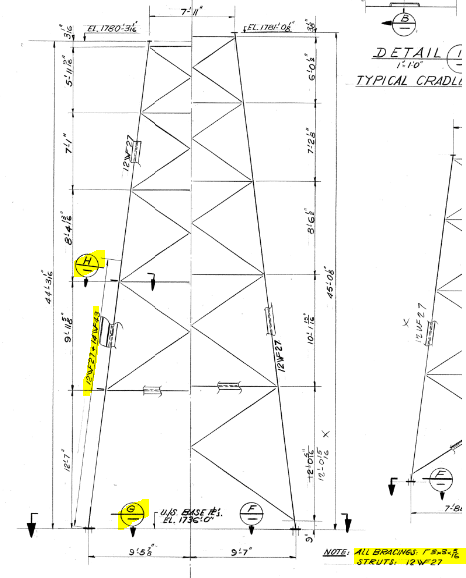
Thanks, CS12