sh3rlock.holmes
Mechanical
- Sep 24, 2024
- 8
Hello Engineers,
My first post here. We are in the process of designing a custom machine, in which power from a motor has to be distributed to 4 shafts, while the axis of the shafts themselves rotate around a central axis. I hope it is clear from the picture attached.
For this purpose, we need a suitable gearbox. At the present moment, we are looking at a 4-way bevel gearbox, (again attached as picture). From the theory I know, this should theoretically work, since the housing of the gearbox can rotate in the central axis, and the shafts can rotate in their axes.
But I think the gearboxes are not designed with such an application in mind. The usual use case is to fix/mount the housing to a stationary body.
So my question is, first of all, do you see any problems with this application, and are there other/special gearboxes that are designed specifically for this purpose?
EDIT : OK I forgot to add a key point. As mentioned before, the 4 shafts and the gearbox housing should rotate about a central axis. THIS ROTATION IS EXTERNALLY POWERED BY A DIFFERENT MOTOR. So basically, the housing of the bevel gearbox will be made to rotate at a constant speed via a different motor, and the initial motor whose input shaft is shown in the picture is used to supply torque to the 4 shafts. This torque control must be independent of the overall rotation, hence we are using 2 separate motors.
Thanks to everyone who commented so far. I'm sorry I forgot to mention this key point.
My first post here. We are in the process of designing a custom machine, in which power from a motor has to be distributed to 4 shafts, while the axis of the shafts themselves rotate around a central axis. I hope it is clear from the picture attached.
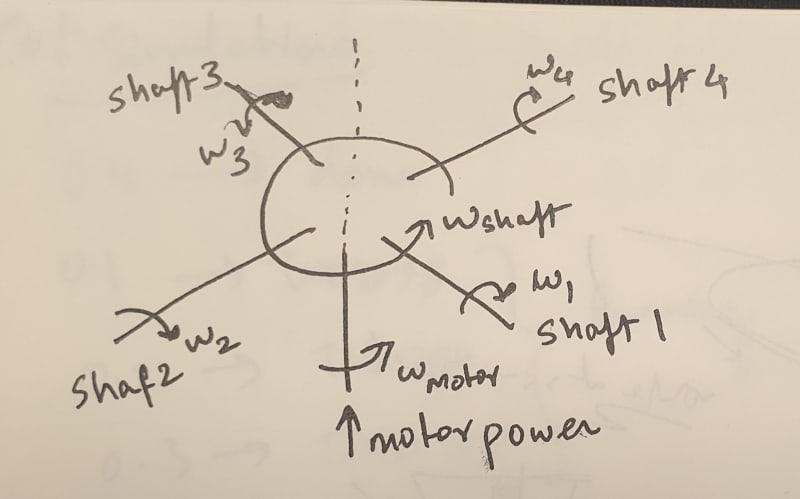
For this purpose, we need a suitable gearbox. At the present moment, we are looking at a 4-way bevel gearbox, (again attached as picture). From the theory I know, this should theoretically work, since the housing of the gearbox can rotate in the central axis, and the shafts can rotate in their axes.
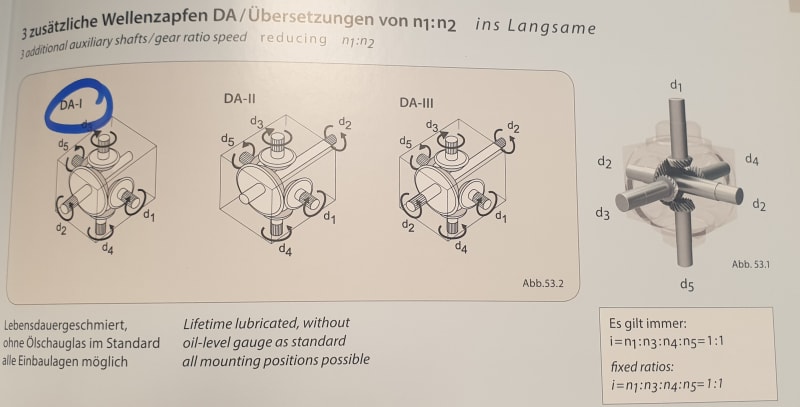
But I think the gearboxes are not designed with such an application in mind. The usual use case is to fix/mount the housing to a stationary body.
So my question is, first of all, do you see any problems with this application, and are there other/special gearboxes that are designed specifically for this purpose?
EDIT : OK I forgot to add a key point. As mentioned before, the 4 shafts and the gearbox housing should rotate about a central axis. THIS ROTATION IS EXTERNALLY POWERED BY A DIFFERENT MOTOR. So basically, the housing of the bevel gearbox will be made to rotate at a constant speed via a different motor, and the initial motor whose input shaft is shown in the picture is used to supply torque to the 4 shafts. This torque control must be independent of the overall rotation, hence we are using 2 separate motors.
Thanks to everyone who commented so far. I'm sorry I forgot to mention this key point.