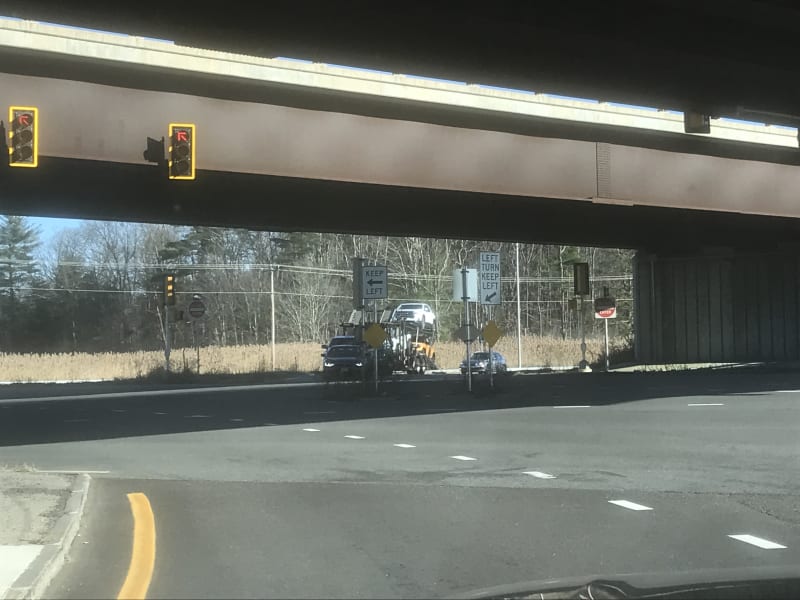
I drive under this on my way to work every day and have always been curious about it. My boss told me, at the time this bridge was built, these were the deepest wide-flange girders in the world (or maybe it was just the U.S.?). At first, I thought it was just the bridge above me casting a wavy shadow, but all 4 girders appear like this.
The lighter portions look like a uniform \/\/\/\/\/\/\/\/\/\/\/\/ strain. My guess is the darker and lighter portions of the flange are deflecting outward opposite of one another. Is this a defect from the fabrication process?
Located in NH by the way.