Kom3
Structural
- Nov 20, 2019
- 37
Hello all,
I have an existing frame as seen in the attached image. Under dead load, the column is overloaded due to weak axis bending. However, if I model the beam as pinned to the column, the bending in the column decreases quite substantially. The bending in the beam goes up since it is now a simple connection but is still underutilized. Would it be okay to model this connection as pinned? For context, this is a solo pipe rack. It is a frame in the transverse direction and an inverted pendulum in the longitudinal direction (not connected to any other frames/bents).
Thanks!
I have an existing frame as seen in the attached image. Under dead load, the column is overloaded due to weak axis bending. However, if I model the beam as pinned to the column, the bending in the column decreases quite substantially. The bending in the beam goes up since it is now a simple connection but is still underutilized. Would it be okay to model this connection as pinned? For context, this is a solo pipe rack. It is a frame in the transverse direction and an inverted pendulum in the longitudinal direction (not connected to any other frames/bents).
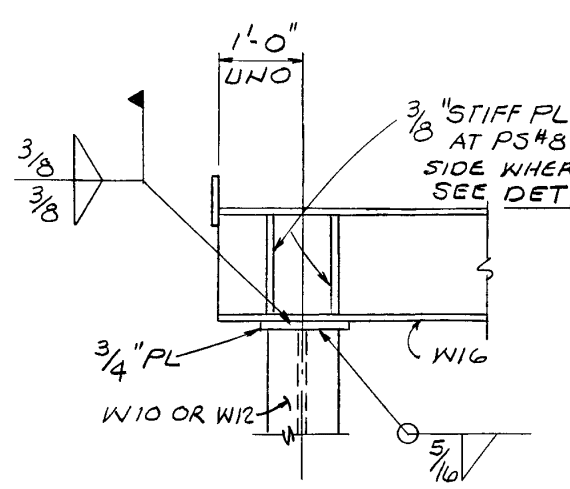
Thanks!