eli28
Aerospace
- Oct 20, 2019
- 109
Hello,
I looked at an existing design of a linear guiding that is actually working and I couldn't believe it.
Here is a picture of the design concept so you might better understand :
Here is a picture of a simplified drawing (forgive me it's far from being perfect) so you might better understand what sizes and precisions we are talking about:
What really made me wonder how it actually works is the fact that the parts are manufactured separately and independently.
When I roughly calculated the optional deviation of the pin when we look at its tip I saw that a position of a hundredths mm may lead to a tenths mm deviation in the far side, where the guided upper plate is being interfaced, and theoretically it should stuck.
I would like to know what is the right design when we need a tight guiding.
it seems that if we manufacture the parts separately with realistic tolerances we have no chance to succeed.
I looked at an existing design of a linear guiding that is actually working and I couldn't believe it.
Here is a picture of the design concept so you might better understand :
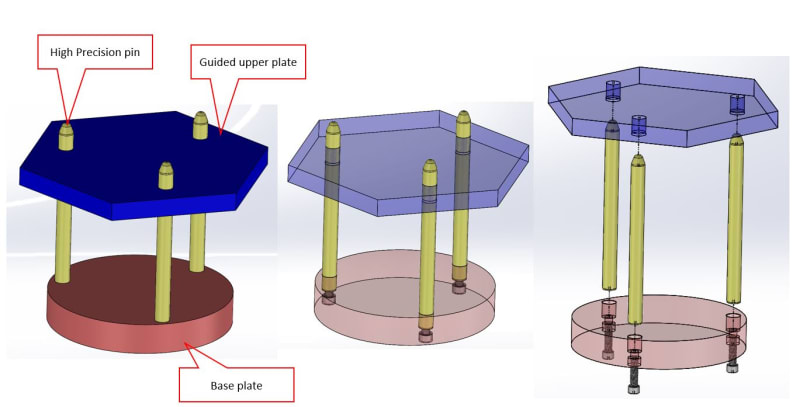
Here is a picture of a simplified drawing (forgive me it's far from being perfect) so you might better understand what sizes and precisions we are talking about:
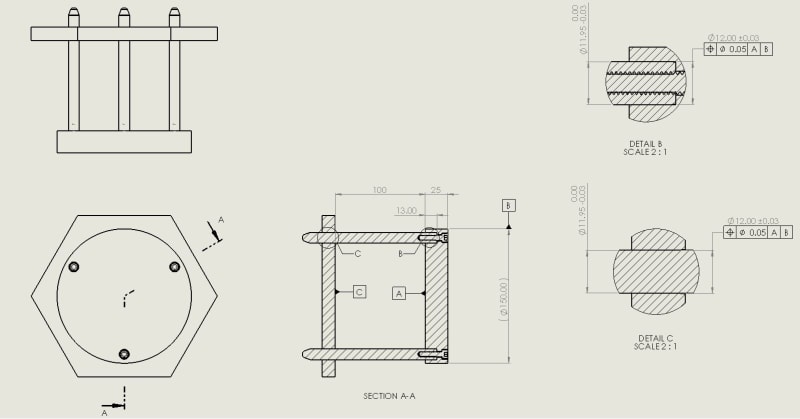
What really made me wonder how it actually works is the fact that the parts are manufactured separately and independently.
When I roughly calculated the optional deviation of the pin when we look at its tip I saw that a position of a hundredths mm may lead to a tenths mm deviation in the far side, where the guided upper plate is being interfaced, and theoretically it should stuck.
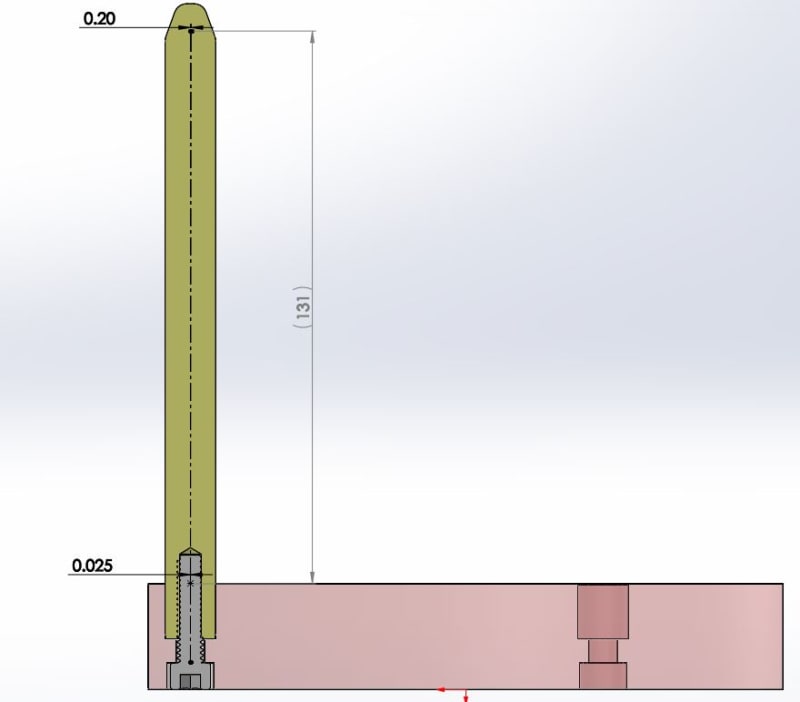
I would like to know what is the right design when we need a tight guiding.
it seems that if we manufacture the parts separately with realistic tolerances we have no chance to succeed.