Bhotar3
Civil/Environmental
- May 6, 2013
- 62
The client wants to demo an existing Veranda over the entrance to a Rigid Frame PEMB, and erect a 30 ft canopy that extends over and covers parking spaces. The column lines are 28 ft apart, and are the main supports for the existing veranda. The would prefer not to drop columns and pour footings, so I would need to design this canopy to connect to the existing tapered columns. For me, I'm not comfortable attaching to the metal building unless I can do an analysis on the entire structure. Only problem is, after contacting the original Architect and EOR, no structural drawings with any existing member sizescan be found,(Shocker, right?), so the only way to determine existing member sizes would be field discovery. Regardless of existing member sizes, I don't think a 30 ft cantilever is feasible, and would most certainly require - at a minimum - columns near midspan (They can't have columns in the parking lot).
What are your opinions of this? Would you feel comfortable designing something connected to existing columns, or would you want to drop 4 columns with 2 adjacent to the existing structure and leave the PEMB untouched??
I have attached sketches for reference, with the existing veranda hatched out.
What are your opinions of this? Would you feel comfortable designing something connected to existing columns, or would you want to drop 4 columns with 2 adjacent to the existing structure and leave the PEMB untouched??
I have attached sketches for reference, with the existing veranda hatched out.
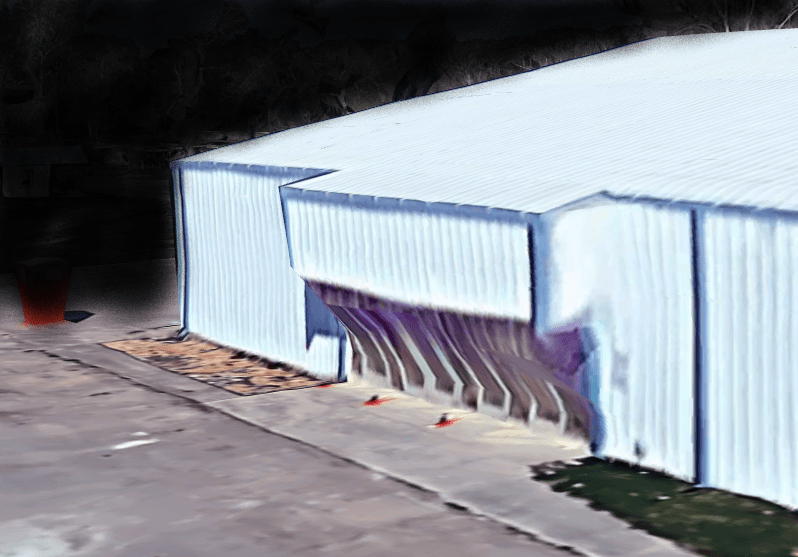
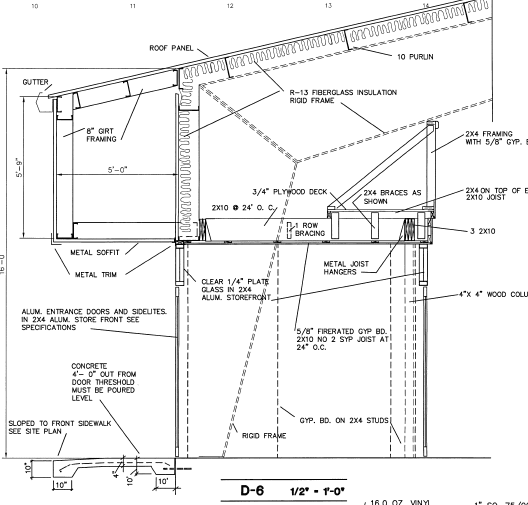
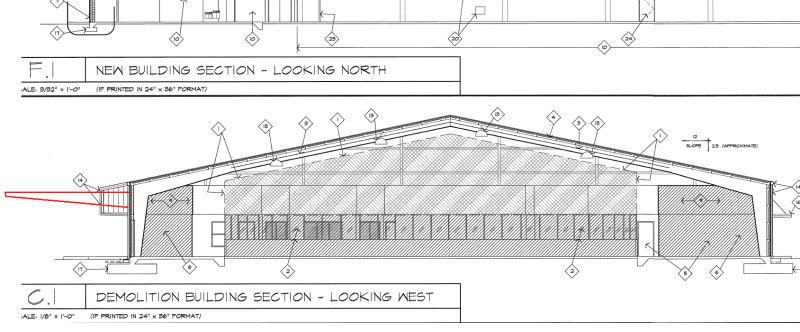
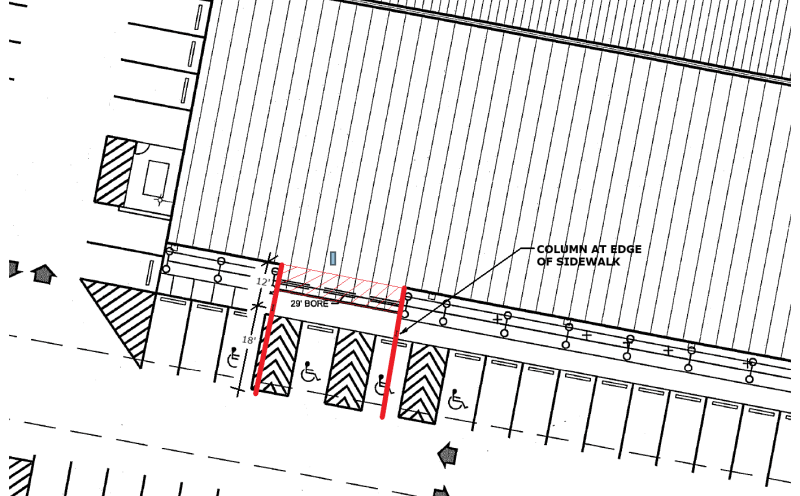