JoelTXCive
Civil/Environmental
I'm designing some larger cantilever retaining walls that will have ~24ft of earth retained. I have an old 'go-by' project from 20 years ago and two things caught my eye (see below image). The wall below is a wing wall for a pump station headwall, and has a total height of 27' ft. The heel is small because overturning was not an issue due to other geometry.
Issue #1: Regardless of bar size, the lower bars at each segment end are not fully developed all the way to the top of the wall segment. You could do 180 hooks, or headed bars to improve the situation, but you still would not be fully developed all the way to the very tippy top of the wall segment, which would mean the moment capacity would be impaired there. Do you agree?
Issue #2: The bars between the segments are not lapped together. They are greater than 6" inches apart, which would be the maximum distance they could ever be apart if you wanted a non-contact lap splice. Maybe these bars do not need to be lapped though? If the lower bar was fully developed all the way to the end, and then the upper bar was embedded the full development length then this would be acceptable. The problem is, the lower is not fully developed (see issue 1 above).
What are your thoughts? And what could I do to improve?
Issue #1: Regardless of bar size, the lower bars at each segment end are not fully developed all the way to the top of the wall segment. You could do 180 hooks, or headed bars to improve the situation, but you still would not be fully developed all the way to the very tippy top of the wall segment, which would mean the moment capacity would be impaired there. Do you agree?
Issue #2: The bars between the segments are not lapped together. They are greater than 6" inches apart, which would be the maximum distance they could ever be apart if you wanted a non-contact lap splice. Maybe these bars do not need to be lapped though? If the lower bar was fully developed all the way to the end, and then the upper bar was embedded the full development length then this would be acceptable. The problem is, the lower is not fully developed (see issue 1 above).
What are your thoughts? And what could I do to improve?
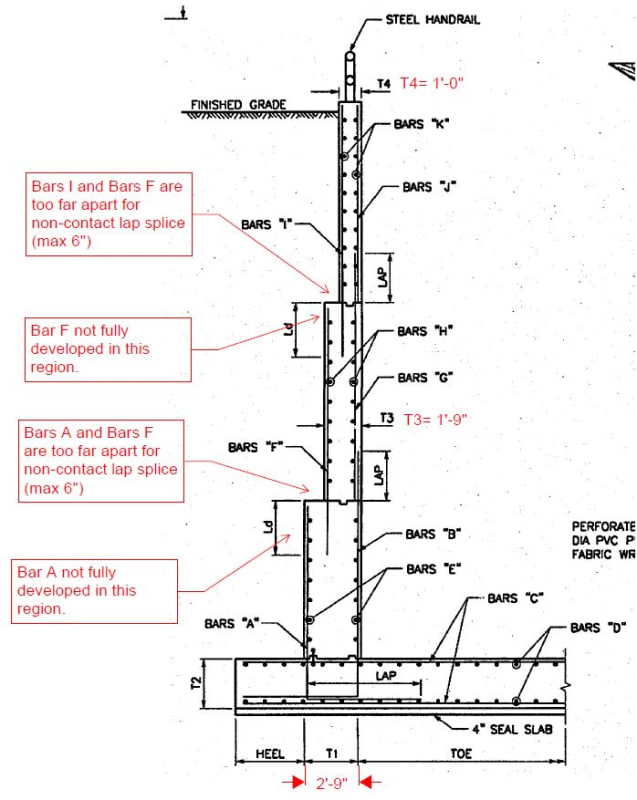