Hello,
I am designing a "cascading" thermal relief system for an oil storage terminal.
The cascade will terminate at an atmospheric storage tank.
Product level in the tank will be variable and as such the "static" back pressure will vary.
See an example sketch below:
My questions are:
a) Does TRV-2 need to be of balanced type due to the variable back pressure (only source of back pressure would be the varying tank head).
b) Is the following approach correct: Assuming TRV-2 is of balanced type and its set pressure is 10 barg. Then the maximum backpressure seen by TRV-1 will be 10barg. If TRV-1 is then specified as balanced valve too, then its minimum set pressure shall be >20 barg (so that the backpressure is <50% of the set pressure as stipulated in API521)?
I'm looking forward to your advice
I am designing a "cascading" thermal relief system for an oil storage terminal.
The cascade will terminate at an atmospheric storage tank.
Product level in the tank will be variable and as such the "static" back pressure will vary.
See an example sketch below:
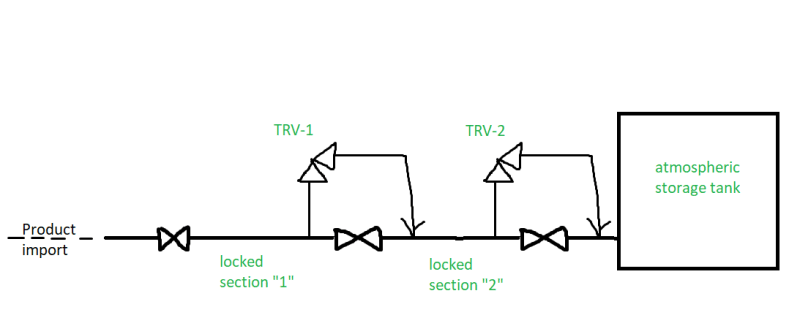
My questions are:
a) Does TRV-2 need to be of balanced type due to the variable back pressure (only source of back pressure would be the varying tank head).
b) Is the following approach correct: Assuming TRV-2 is of balanced type and its set pressure is 10 barg. Then the maximum backpressure seen by TRV-1 will be 10barg. If TRV-1 is then specified as balanced valve too, then its minimum set pressure shall be >20 barg (so that the backpressure is <50% of the set pressure as stipulated in API521)?
I'm looking forward to your advice
