emonje
Mechanical
- Nov 3, 2006
- 48
This is a cast steel spelter socket. Failed after 24 hours of service.
Trying to guess what might have been the issue before sending out for tests.
Fracture started here??:
Other side of the same leg. Gas porosities??:
The legs are bent, yielding after fracture??:
Also these opened up on one of the legs:
Any observation is highly appreciated.
Thanks.
Trying to guess what might have been the issue before sending out for tests.
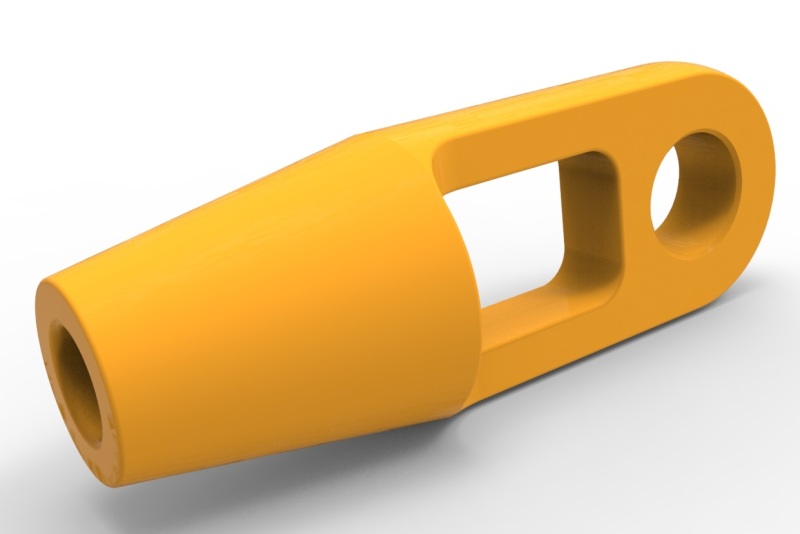
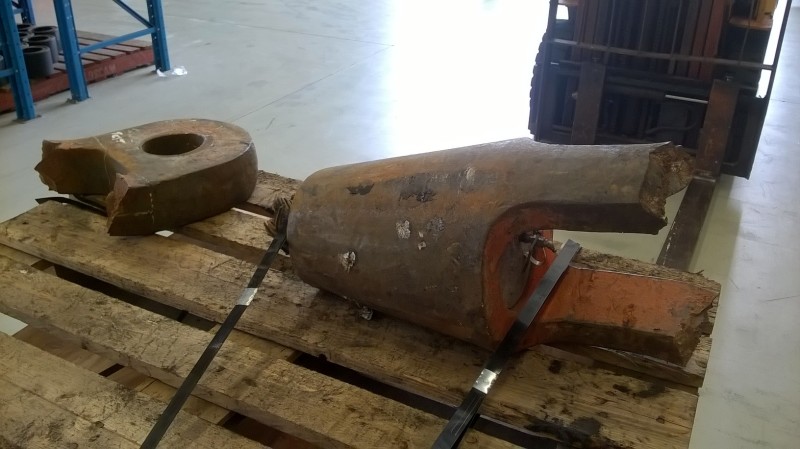

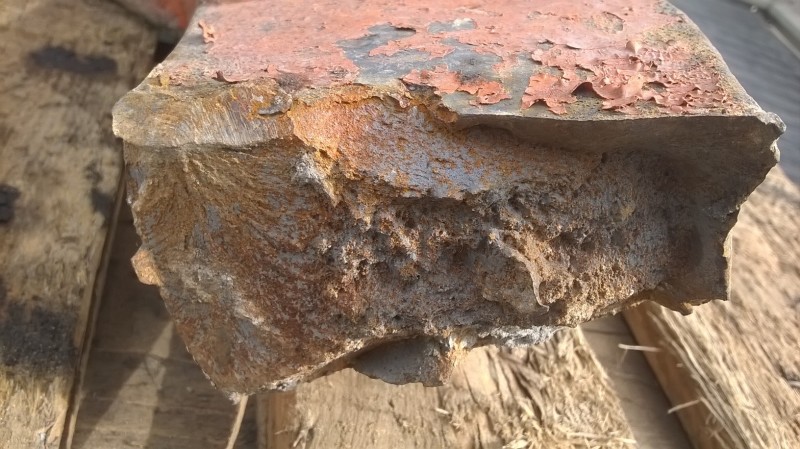
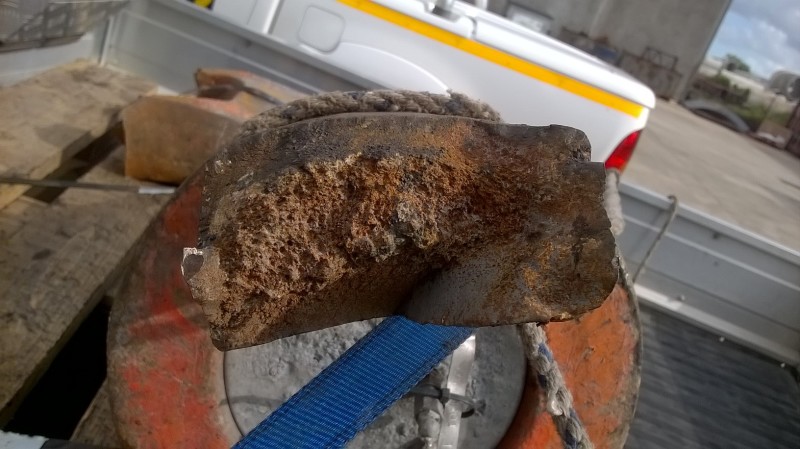
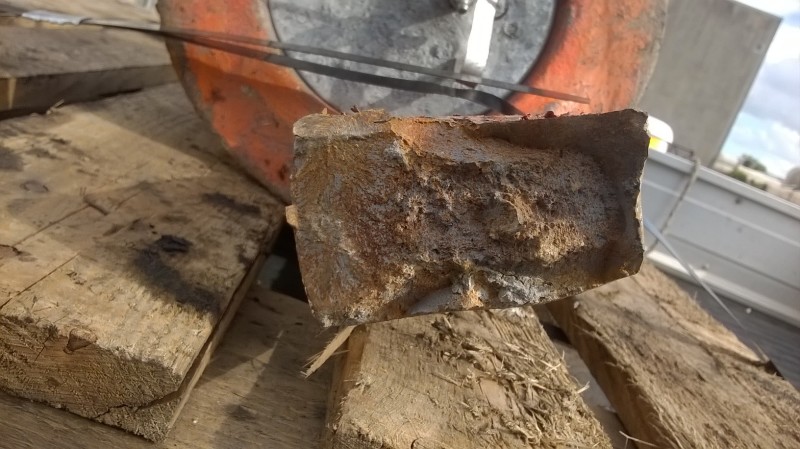
Fracture started here??:
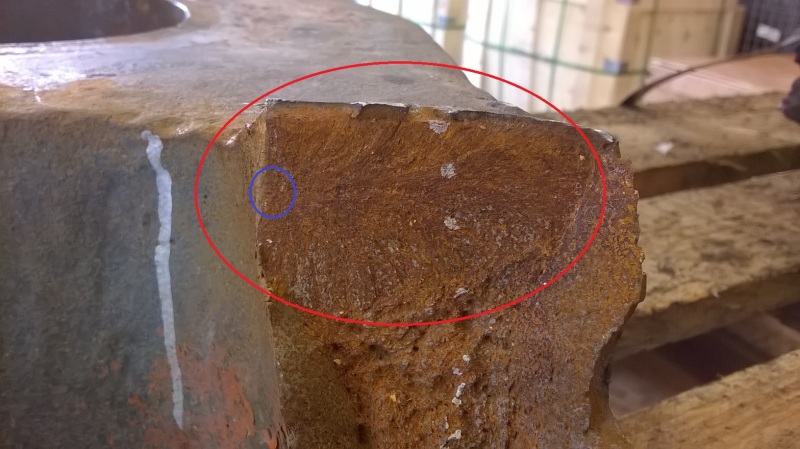
Other side of the same leg. Gas porosities??:
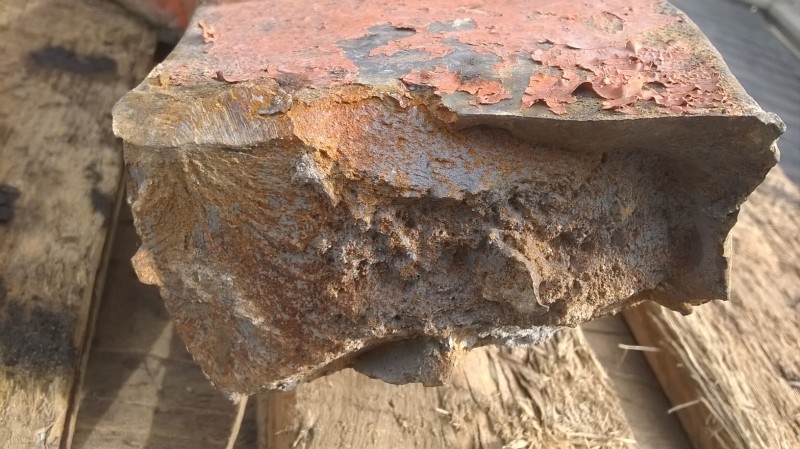
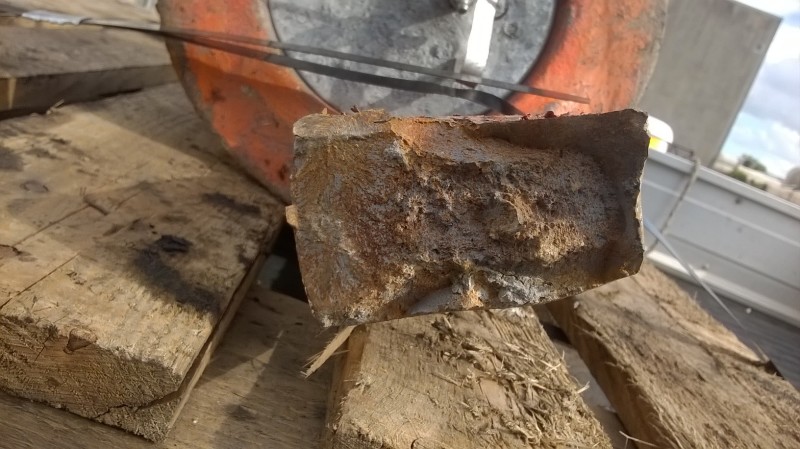
The legs are bent, yielding after fracture??:
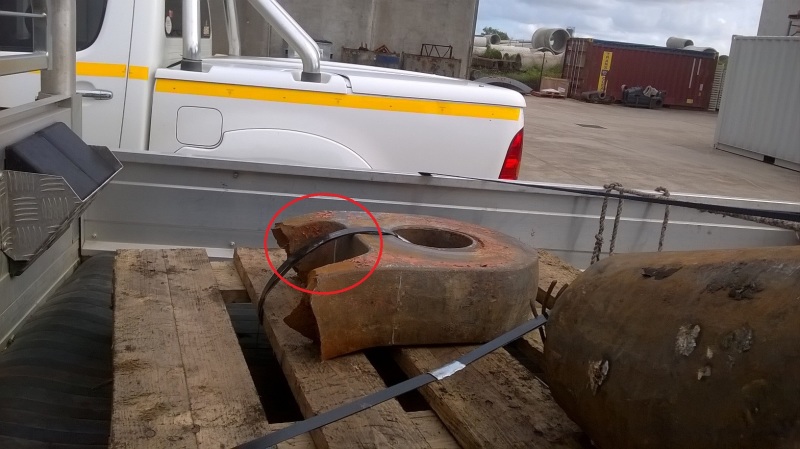
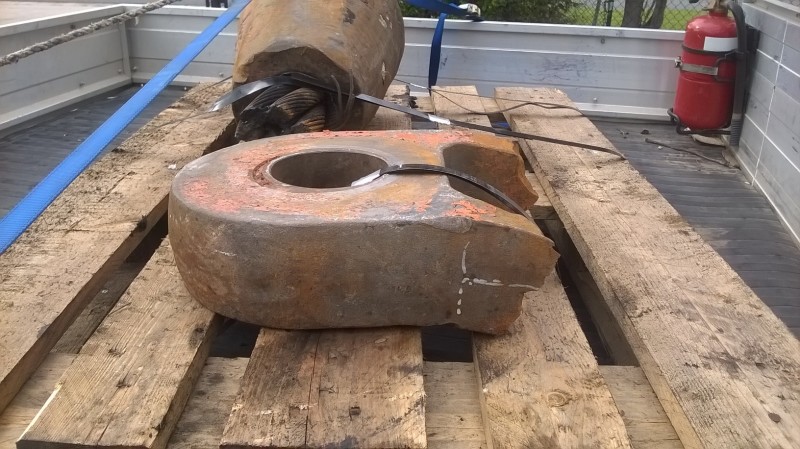
Also these opened up on one of the legs:
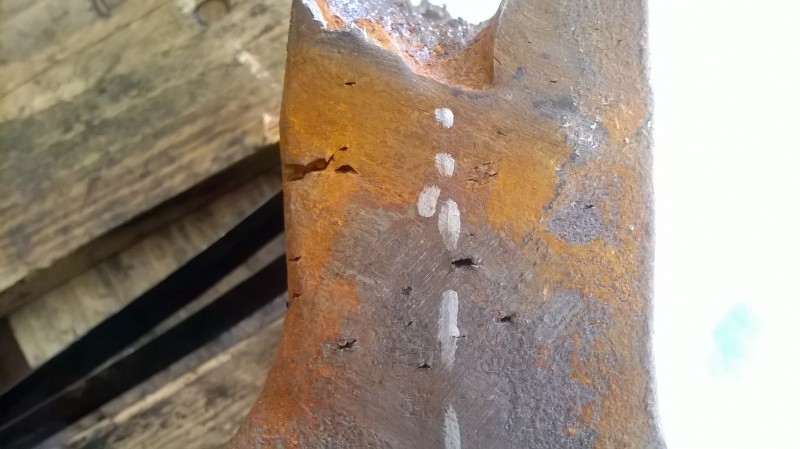
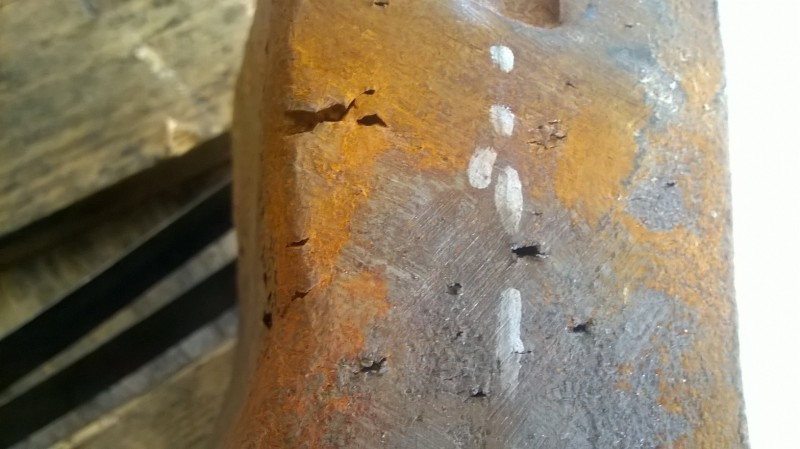
Any observation is highly appreciated.
Thanks.