Skinnattittar
Civil/Environmental
Hopefully this has not been asked too many times on these forums, but I have a gable wall on a building with a cathedral ceiling (see pic) where the framer did not make the studs full height.
Our plans do not specifically call out the requirement that the studs be full height and the contractor is saying it is our fault for not tell them and their framers that they could not build this wall the way they did. Our general notes do not specifically address this sort of issue, but do call out that the project is to be built in accordance with IBC 2015 and NDS 2015 with an additional note "... all framing shall be plumb, true, and adequately braced such that the structure is rigid..." (not my choice, but I'm not in charge here...).
I've only done some google searches, but I'm not finding anything explicit in either that dictate full height studs or bracing the wall (though I feel like I have in the past...). I've flipped through my construction guidebooks and some googling, and the only time this sort of detail is addressed (as it is shown in the pic) is to say "don't do this" but I don't see a reference to any code. So my question is; is there?
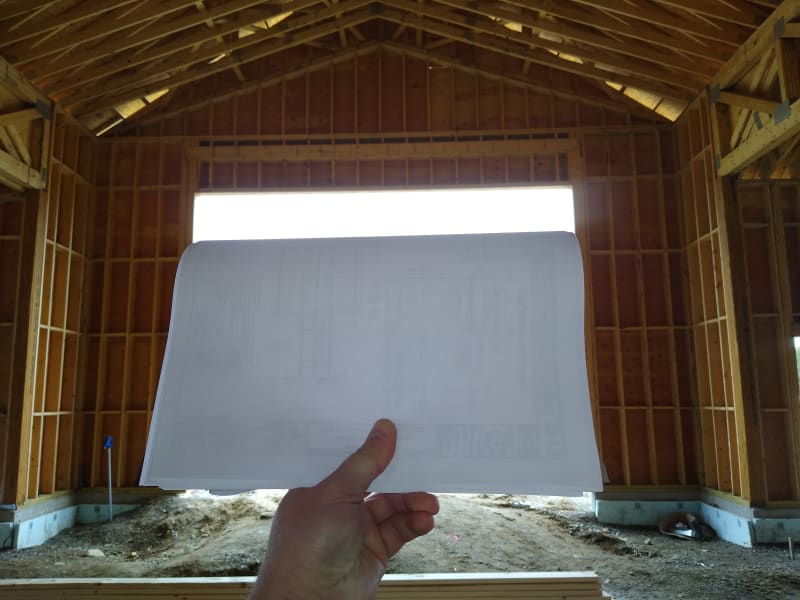
Our plans do not specifically call out the requirement that the studs be full height and the contractor is saying it is our fault for not tell them and their framers that they could not build this wall the way they did. Our general notes do not specifically address this sort of issue, but do call out that the project is to be built in accordance with IBC 2015 and NDS 2015 with an additional note "... all framing shall be plumb, true, and adequately braced such that the structure is rigid..." (not my choice, but I'm not in charge here...).
I've only done some google searches, but I'm not finding anything explicit in either that dictate full height studs or bracing the wall (though I feel like I have in the past...). I've flipped through my construction guidebooks and some googling, and the only time this sort of detail is addressed (as it is shown in the pic) is to say "don't do this" but I don't see a reference to any code. So my question is; is there?