Hi to all colleagues out there,
In the ethylene plant that company where I work is biulding there are three ITT Goulds Non-API pumps OH1, namely P-1234A/B/C, running with equalized water, rated capacity each one 300m3/h@40.3m.
There are several operating cases, but the normal one requires two pumps running in parallel. When we run pump A and B, the pump B is having a higher vibration than A. When runs B and C, again B has higher vibration than C. Last case is when A and C runs in parallel both has similar vibration and under normal ISO limits for newly commisioning machines. in the physical arrangement the pump B is in the middle, and suction piping layout is not symetrical. I have attached a snapshot of the 3D. Vibration measurements found 4X component. Also, found sort of cyclic sound coming from the piping. Current absorption of pump motor B is lower than other two motors.
my first thought is that 4X is coming from vane pass frequency due to operation too much to the left of BEP which is somehow confirmed by current absoption being less than other pumps. However I dont have any explanation of why this happens only with one pump. someone suggested the problem comes from the suction piping layout.
Any ideas of why only one pump is having this behaviour and any suggestions of how to solve? Client wants to rotate the two pumps in operation to have "uniform" wear in all the three pumps so now I need to find a way to reduce vibration of pump B.
Appreciate any support.
In the ethylene plant that company where I work is biulding there are three ITT Goulds Non-API pumps OH1, namely P-1234A/B/C, running with equalized water, rated capacity each one 300m3/h@40.3m.
There are several operating cases, but the normal one requires two pumps running in parallel. When we run pump A and B, the pump B is having a higher vibration than A. When runs B and C, again B has higher vibration than C. Last case is when A and C runs in parallel both has similar vibration and under normal ISO limits for newly commisioning machines. in the physical arrangement the pump B is in the middle, and suction piping layout is not symetrical. I have attached a snapshot of the 3D. Vibration measurements found 4X component. Also, found sort of cyclic sound coming from the piping. Current absorption of pump motor B is lower than other two motors.
my first thought is that 4X is coming from vane pass frequency due to operation too much to the left of BEP which is somehow confirmed by current absoption being less than other pumps. However I dont have any explanation of why this happens only with one pump. someone suggested the problem comes from the suction piping layout.
Any ideas of why only one pump is having this behaviour and any suggestions of how to solve? Client wants to rotate the two pumps in operation to have "uniform" wear in all the three pumps so now I need to find a way to reduce vibration of pump B.
Appreciate any support.
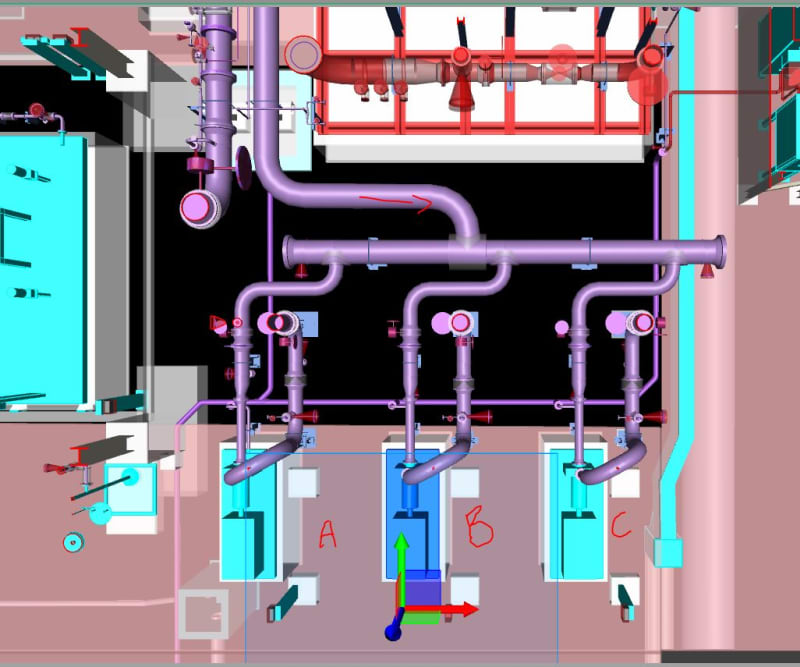
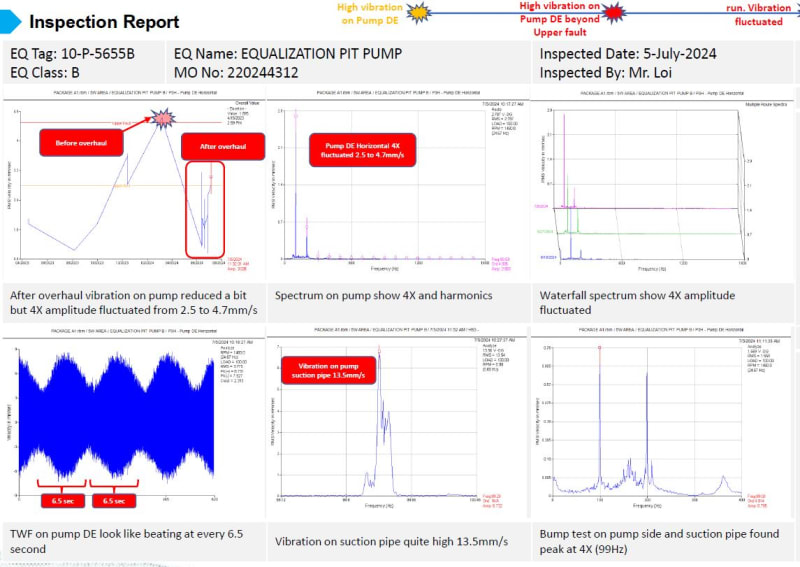