PROFR
Structural
- Feb 28, 2019
- 33
We are building a vertical metal deck wall behind a masonry wall that will be taking an earth pressure as shown to strengthen it. We are temporary screwing the metal deck to the wall and then installing the steel columns to laterally support the metal deck. We need to tie the deck to the flanges of the column to laterally support the flange. Typical deck screws will not work because they cannot be done from the other side of the deck. What is the best to do to attached the deck to the flange? bolts? screws? weld?
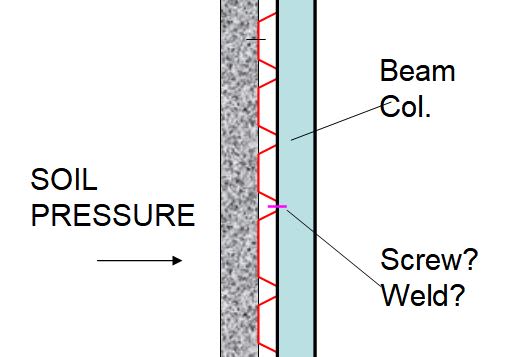