Hello everyone.
I encountered a problem related to pipeline compensation as you can see in the attached picture. This is an installation project from an external contractor. The green arrows represent the sliding supports. Pipe size 6 in. Temperature rise 180 K. Stainless steel tube. Do I understand correctly that a pipeline sized 1500mm will extend approximately 5mm in the direction shown (blue arrow) and will act on the perpendicular pipe 740mm from the sliding support (probably leading to failure)?
I kindly ask for an explanation. Unfortunately, I am completely unfamiliar with compensation topics. Sorry for the poor paint sketch.
Regards
I encountered a problem related to pipeline compensation as you can see in the attached picture. This is an installation project from an external contractor. The green arrows represent the sliding supports. Pipe size 6 in. Temperature rise 180 K. Stainless steel tube. Do I understand correctly that a pipeline sized 1500mm will extend approximately 5mm in the direction shown (blue arrow) and will act on the perpendicular pipe 740mm from the sliding support (probably leading to failure)?
I kindly ask for an explanation. Unfortunately, I am completely unfamiliar with compensation topics. Sorry for the poor paint sketch.
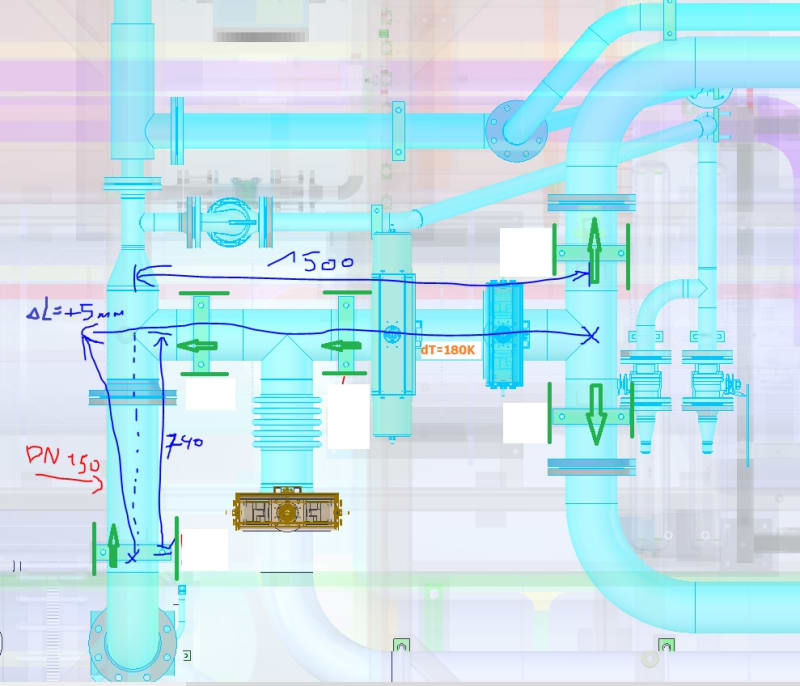
Regards