2020Learner
Automotive
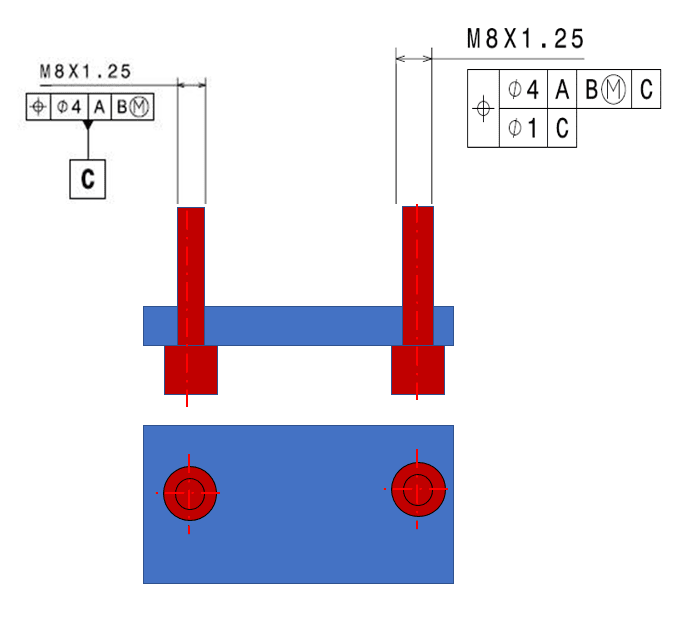
Hello Team,
I have one doubt regarding composite position tolerance- Inserted picture.
This is an Assembly where Datum A & Datum B is at inlet side and I shown picture at only other end where we can see Datum C is applied to one of the stud in the flange.
Other single stud is controlled with composite positional tolerance with respect to Datum C, which is applied to other Stud.
What I know from my experience is that Composite tolerance is applicable for pattern, so here we have two stud, one is Datum C and for single stud is applied with Composite position.
I felt it is wrongly interpreted here, lower segment is controlled with Datum C in composite frame. Can you all agree or do we have anything like this in ISO application or etc.?
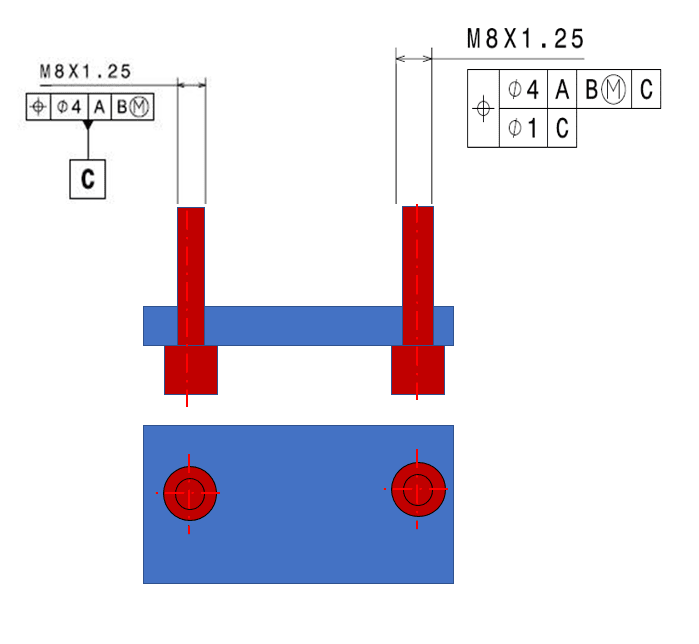