I have a SR machined into the top of a block. The bottom is datum A, the long side datum B and the short side datum C. Basic dimensions are given from each of these faces. We have profile of .020 but want to refine the shape to be within .005
For a composite tolerance I know the top line locks location and rotation. The bottom line controls rotation only. My question is, on the bottom line do I control it to A B and C or just B and C. None of the planes go thru the sphere.
Would this differ if datum B and C had been center planes with the SR having a basic of 0 to both B and C but still offset from A?
________________________________
Ryan
3d Printing
Laser Cutting
CNC Milling
For a composite tolerance I know the top line locks location and rotation. The bottom line controls rotation only. My question is, on the bottom line do I control it to A B and C or just B and C. None of the planes go thru the sphere.
Would this differ if datum B and C had been center planes with the SR having a basic of 0 to both B and C but still offset from A?
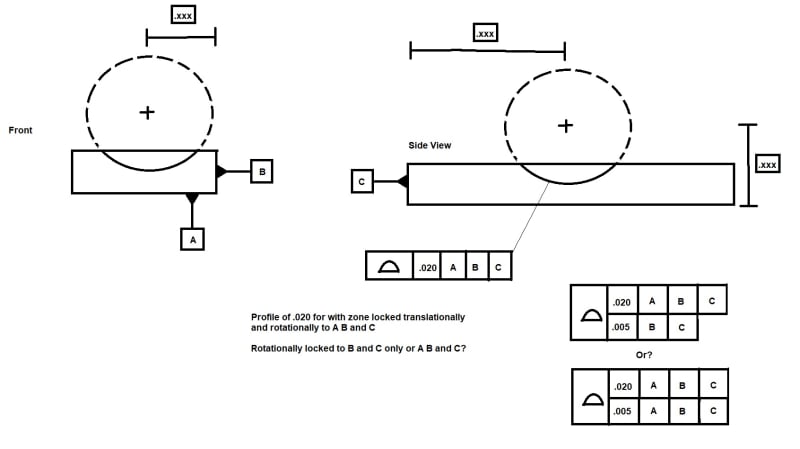
________________________________
Ryan
3d Printing
Laser Cutting
CNC Milling