JoelTXCive
Civil/Environmental
- Jul 24, 2016
- 933
I have a question regarding concrete corbels similar to below........
Are Corbels like this generally cast with the wall, or are they cast in a secondary pour?
Background:
I have a pump station wall that is going to support some concrete beams. The wall geometry is tough, so I'm worried about the contractor being able to cast the wall with dowels in the correct place.
The floor below the wall slopes at about ~10%; and the top of wall slope will not be parallel. The line of supported beams will not be parallel to either the top of wall or the bottom of wall.
I'm thinking, I could leave some ~2ft x 2ft blockouts in the wall when it is cast. I would have the wall bars continuous across the blocked out opening.
Then, the contractor can weave in their bars for the corbels in exactly the correct spot; and a secondary pour may be made for the corbel?
I'm open to input.
Thank you!
Are Corbels like this generally cast with the wall, or are they cast in a secondary pour?
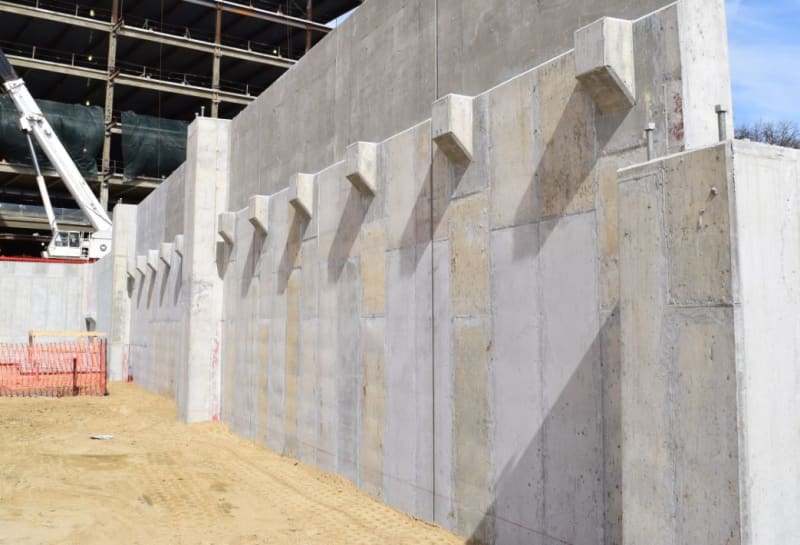
Background:
I have a pump station wall that is going to support some concrete beams. The wall geometry is tough, so I'm worried about the contractor being able to cast the wall with dowels in the correct place.
The floor below the wall slopes at about ~10%; and the top of wall slope will not be parallel. The line of supported beams will not be parallel to either the top of wall or the bottom of wall.
I'm thinking, I could leave some ~2ft x 2ft blockouts in the wall when it is cast. I would have the wall bars continuous across the blocked out opening.
Then, the contractor can weave in their bars for the corbels in exactly the correct spot; and a secondary pour may be made for the corbel?
I'm open to input.
Thank you!