BridgeEngineer21
Structural
- Oct 26, 2021
- 58
I am working on an anchorage design in accordance with Eurocode. In cases where Eurocode is unclear, I can refer to other sources, and in extreme cases I can apply for a waiver of a code requirement if I have a good justification to do it an alternate way. So, here is the situation at issue:
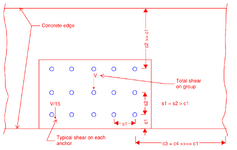
The relevant Eurocode clauses for concrete edge failure:
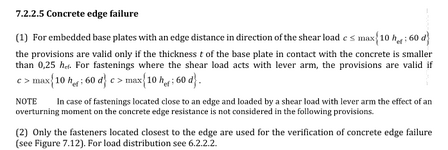
From 6.2.2.2:
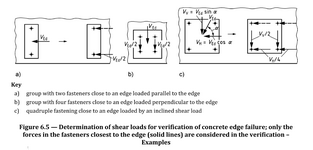
I think its pretty clear Eurocode requires me to check this edge failure area against the full shear force:
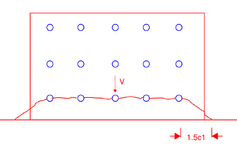
Now if I look at ACI, this situation would warrant the following 2 cases to be checked:
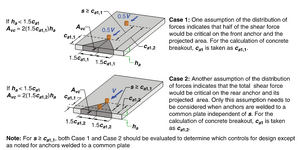
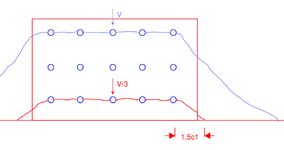
Clearly, the Eurocode check is much more conservative, and in this case is causing serious problems.
Now, I'm also referring to a very helpful reference book: Anchorage in Concrete Construction, First edition (R. Eligehausen, R. Mallee, J. F. Silva). I don't know the history exactly, but it seems that a lot of the research and explanations adopted in this document are incorporated in both Eurocode 1992-4 and ACI 318. (In general, ACI seems to more explicitly state some of the explanations and reasoning from this reference in the commentary column).
I'm sharing a couple of pages attached in case anyone is interested in some more reading, but essentially the book agrees with the ACI reference manual. This figure below is particularly illustrative, and this part of the text was persuasive to me: "If the shear load is initially resisted by the near-edge anchor alone, it will generate a concrete breakout crack. Following displacement sufficient to bring the rear anchor into a bearing condition, that anchor will then resist the entire shear load.
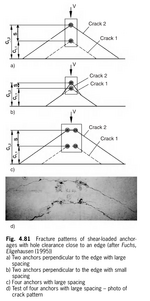
Now, the question I have for all of you is if you can think of a persuasive argument why the Eurocode assumption on shear distribution should be adopted over the ACI/reference manual assumption, other than "just cause" it's more conservative.
Appreciate any input!
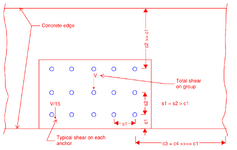
The relevant Eurocode clauses for concrete edge failure:
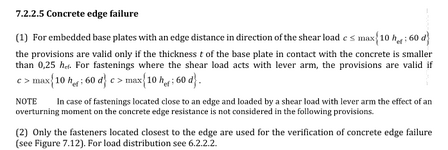
From 6.2.2.2:
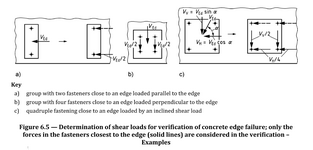
I think its pretty clear Eurocode requires me to check this edge failure area against the full shear force:
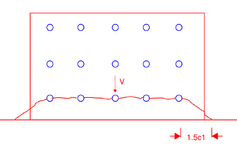
Now if I look at ACI, this situation would warrant the following 2 cases to be checked:
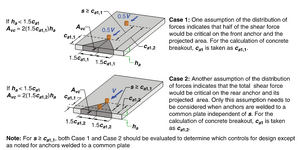
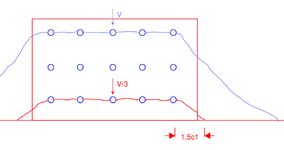
Clearly, the Eurocode check is much more conservative, and in this case is causing serious problems.
Now, I'm also referring to a very helpful reference book: Anchorage in Concrete Construction, First edition (R. Eligehausen, R. Mallee, J. F. Silva). I don't know the history exactly, but it seems that a lot of the research and explanations adopted in this document are incorporated in both Eurocode 1992-4 and ACI 318. (In general, ACI seems to more explicitly state some of the explanations and reasoning from this reference in the commentary column).
I'm sharing a couple of pages attached in case anyone is interested in some more reading, but essentially the book agrees with the ACI reference manual. This figure below is particularly illustrative, and this part of the text was persuasive to me: "If the shear load is initially resisted by the near-edge anchor alone, it will generate a concrete breakout crack. Following displacement sufficient to bring the rear anchor into a bearing condition, that anchor will then resist the entire shear load.
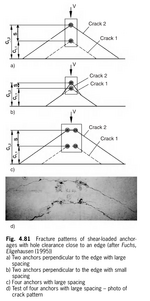
Now, the question I have for all of you is if you can think of a persuasive argument why the Eurocode assumption on shear distribution should be adopted over the ACI/reference manual assumption, other than "just cause" it's more conservative.
Appreciate any input!