dik
Structural
- Apr 13, 2001
- 26,032
Is there a table that gives the gauge required for concrete filled metal pan stair treads. I've seen gauges from 16ga to 10ga used for typical spans of about 3'6 max, with 1-1/2 concrete treads. Something like:
Rather than think climate change and the corona virus as science, think of it as the wrath of God. Feel any better?
-Dik
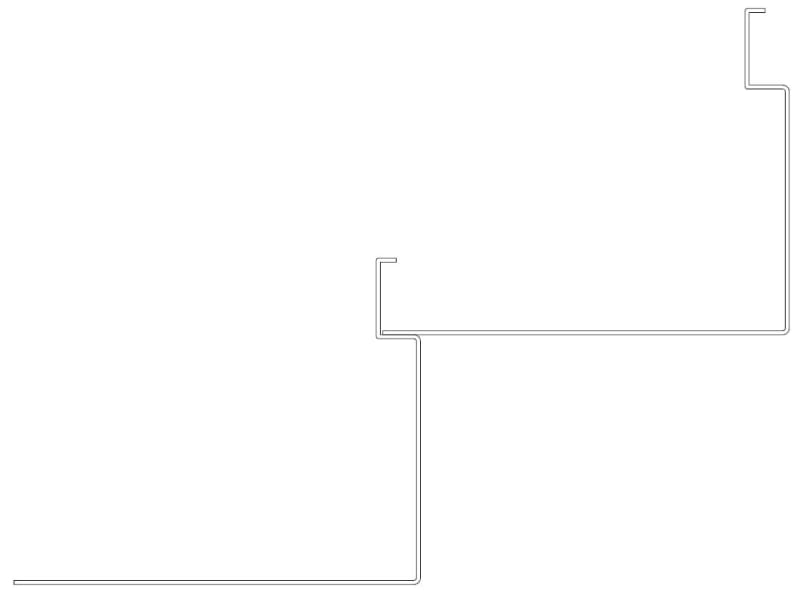
Rather than think climate change and the corona virus as science, think of it as the wrath of God. Feel any better?
-Dik