Eisenhauer
Aerospace
- Nov 18, 2022
- 5
Just wanted to hear your opinions; there is already fighting about whether connectors are called Js or Ps, plugs or sockets, receptacles or plugs and whether male pin connectors can be receptacles or
female contacts means a Jack or it is a matter of what plugs onto what or what totally covers the other....
Generally I try to stick with the following convention (see pic):
[ol 1]
[li]LRU connectors have sequential Jn assignments regardless of what gender the pins or whether the manufacturer calls it receptacle or plug.[/li]
[li]All that plugs into the LRU Js are then Ps (loose ends). Also regardless of gender.[/li]
[/ol]
Now with that out of the way how would you go about numbering the mating connectors in the system wiring harness that may comprise several individual cable assys, some ends may have interfaces to the aircraft (meaning in a wiring diagram issued to an installer before they will likely get re-named by them iaw. their own conventions).[/li]
Would you start each cable assembly having its connectors named P1, P2, P3 regardless of where they plug into?
In other words a P1 could plug into a J2 - making some people uncomfortable.
One could also number them (regardless of what assy they belong to) sequentially that there will never be two P1s also causing non-matching numbers to mate.
Also there could be two P1s in the overall system harness but in different cable assys, that will also make some people unhappy.
But from my POV however having each cable assy numbered P1 to Pn is the most logical in a presentation, regardless of which LRU J they plug into.
Any comments? Thanks, Mike
Example small system intentionally showing no P numbering:
female contacts means a Jack or it is a matter of what plugs onto what or what totally covers the other....
Generally I try to stick with the following convention (see pic):
[ol 1]
[li]LRU connectors have sequential Jn assignments regardless of what gender the pins or whether the manufacturer calls it receptacle or plug.[/li]
[li]All that plugs into the LRU Js are then Ps (loose ends). Also regardless of gender.[/li]
[/ol]
Now with that out of the way how would you go about numbering the mating connectors in the system wiring harness that may comprise several individual cable assys, some ends may have interfaces to the aircraft (meaning in a wiring diagram issued to an installer before they will likely get re-named by them iaw. their own conventions).[/li]
Would you start each cable assembly having its connectors named P1, P2, P3 regardless of where they plug into?
In other words a P1 could plug into a J2 - making some people uncomfortable.
One could also number them (regardless of what assy they belong to) sequentially that there will never be two P1s also causing non-matching numbers to mate.
Also there could be two P1s in the overall system harness but in different cable assys, that will also make some people unhappy.
But from my POV however having each cable assy numbered P1 to Pn is the most logical in a presentation, regardless of which LRU J they plug into.
Any comments? Thanks, Mike
Example small system intentionally showing no P numbering:
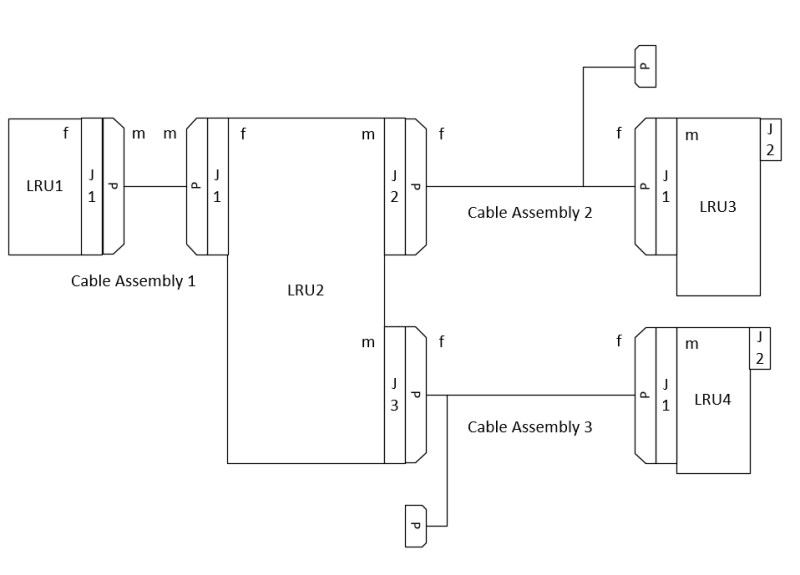