hetgen
Structural
- May 3, 2010
- 221
The detail below is for a 9.0m x 9.0m [30 ft x 30 ft] slab-on-grade (slab on ground) panel, my question is won't that amount of steel across the saw-cut joint completely lock the contraction and risk a random crack to form elsewhere?
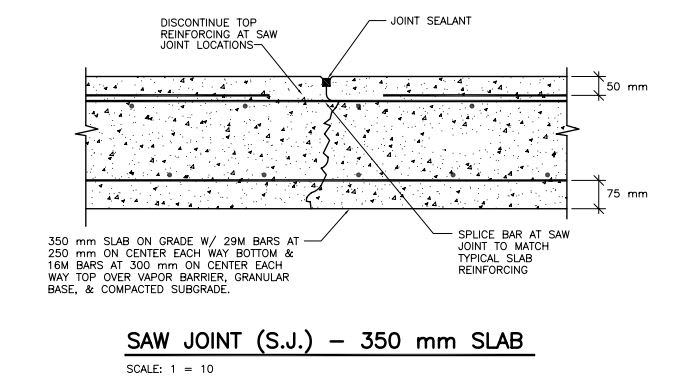