jaytelle
Civil/Environmental
- Dec 15, 2021
- 23
Hello,
I'm an environmental engineer and trying to put together a filter prototype. My ignorance on electrical/controls is monumental. Assume nothing I say is correct.
So basically this is a media bed filter - I attached some images below. There are three motorized ball valves: 1 is a feed valve, 1 is a drain valve, 1 is a filtrate/backwash valve. Below is a brief description.
1) Normal operation, flow goes through V1 and out V2. V3 is closed.
2) If the pressure switch is triggered or an external 24hr timer expires then the unit does an auto clean
My questions are: Is this possible to do with simple timers( I imagine that each of the Qty 8 steps requires a separate timer? Plus Qty 1 24hr timer. Total of 9 timers?
Does this make any sense? Is there a better way for someone who has no control experience to get this done?
Many thanks,
JL
I'm an environmental engineer and trying to put together a filter prototype. My ignorance on electrical/controls is monumental. Assume nothing I say is correct.
So basically this is a media bed filter - I attached some images below. There are three motorized ball valves: 1 is a feed valve, 1 is a drain valve, 1 is a filtrate/backwash valve. Below is a brief description.
1) Normal operation, flow goes through V1 and out V2. V3 is closed.
2) If the pressure switch is triggered or an external 24hr timer expires then the unit does an auto clean
If pressure switch was triggered, it resets 24hr timer
V1 and V2 close (V3 normally closed)
V3 opens to drain the unit (V1 and V2 are closed)
V3 closes (V1 and V2 are closed)
V2 opens to backwash media (V1 and V3 are closed
V2 closes (V1 and V3 are closed)
V3 opens to drain the unit (V1 and V2 are closed)
V3 closes (V1 and V2 are closed)
V1 and V2 open (V3 closed)
3)Return to step 1My questions are: Is this possible to do with simple timers( I imagine that each of the Qty 8 steps requires a separate timer? Plus Qty 1 24hr timer. Total of 9 timers?
Does this make any sense? Is there a better way for someone who has no control experience to get this done?
Many thanks,
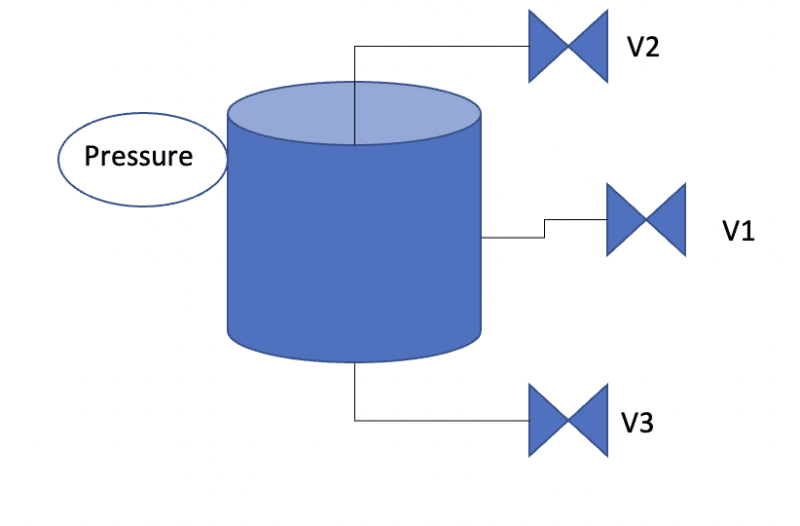
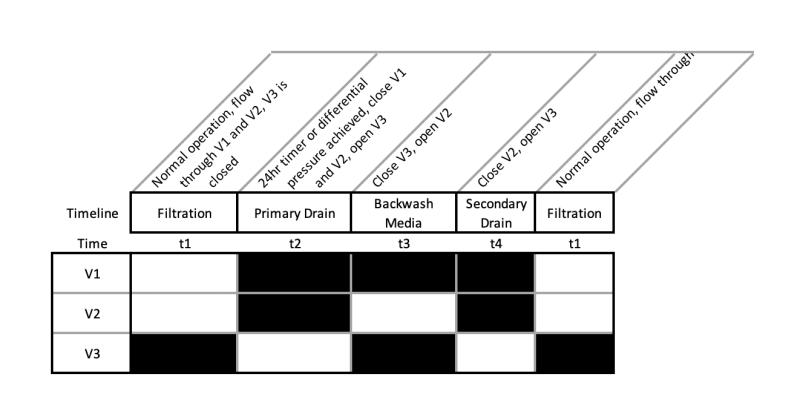
JL