GemmellG
Materials
- Jun 28, 2012
- 89
Developing a Cooper/Nickel(Orbital)welding procedure Material is 4" Sch40 ASTM B466 UNS-C70600 Weld Filler ERCuNi(67). Shielding gas Argon 100% Back Purge Argon 100%. Applying hot pass is were we are having issues. Does anyone have any ideas as I have run out. Attached is a photo of the fit-up & completed root pass. Thanks.
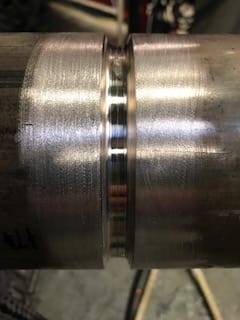
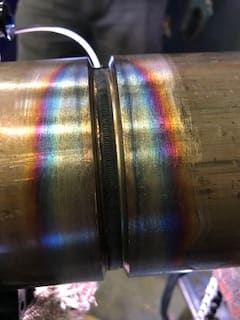