Hello
Please could you advise me with regard to the correct measuring practice for the following air bending patterns to get the correct bend dimensions and angles :
1. 90 degree bend (Edge to bend)
2. Acute angle bend (30 degree) (Edge to bend)
3. Offset 90 degree bend (bend to bend). 2 bending steps
4. Closed and open hem (edge to bend)
5. U bend ( bend to bend). 2 bending steps
Please could you advise me with regard to the correct measuring practice for the following air bending patterns to get the correct bend dimensions and angles :
1. 90 degree bend (Edge to bend)
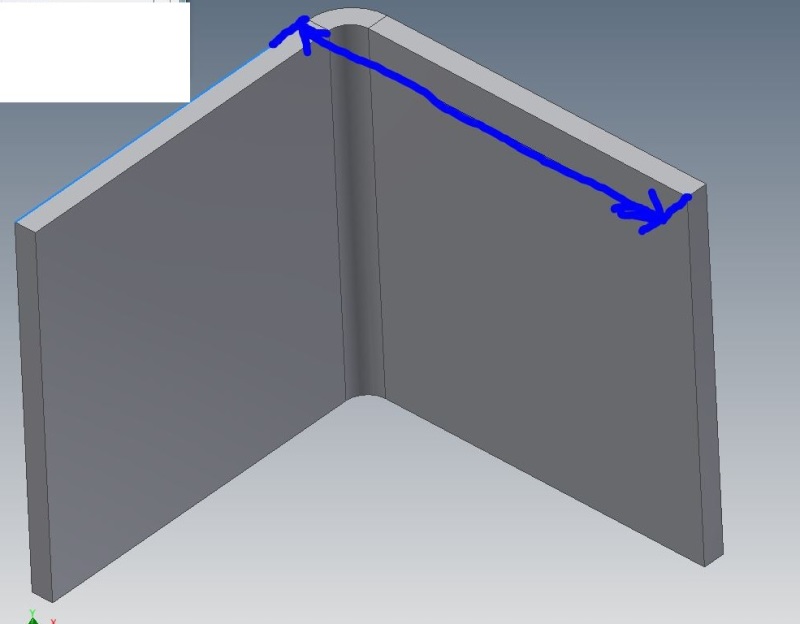
2. Acute angle bend (30 degree) (Edge to bend)
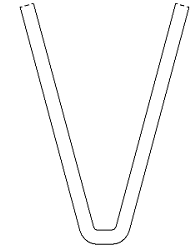
3. Offset 90 degree bend (bend to bend). 2 bending steps
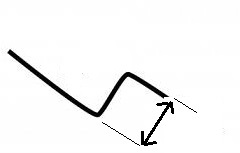
4. Closed and open hem (edge to bend)
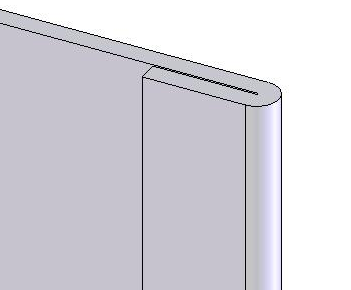
5. U bend ( bend to bend). 2 bending steps
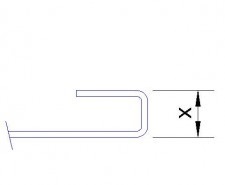