TopPocket
Mechanical
- Feb 16, 2022
- 50
Hi so I have some parts I wish to define. ISO please.
The requirement is that the surface of them must fit within a volume defined by a datum axis. I figured as MMR must be used I will have to use Position rather than Runout or Concentricity.
Now to inspect these I will use a Shadowgraph. They will be rotated with the datum feature in a V block. The horizonal line of the crosshairs will be used to find the highest point along the edge through the rotation. The same will be done to find the lowest point and the difference reported.
I know MMR will not be simple to apply but to be honest I expect to not have to use it except for a few edge cases. It's just there if I need it.
My question is when I define position on the diameter I usually come off the dimension, but doesn't this imply it's to the axis. How do I draw it to indicate it is to the surface or does it not matter? Will this impact whether I put a Ø on the tolerance?
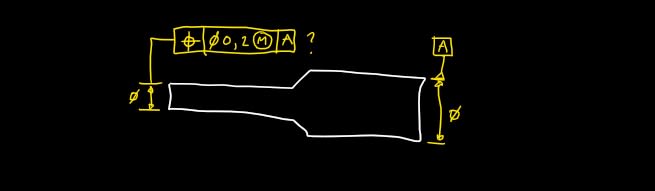
The requirement is that the surface of them must fit within a volume defined by a datum axis. I figured as MMR must be used I will have to use Position rather than Runout or Concentricity.
Now to inspect these I will use a Shadowgraph. They will be rotated with the datum feature in a V block. The horizonal line of the crosshairs will be used to find the highest point along the edge through the rotation. The same will be done to find the lowest point and the difference reported.
I know MMR will not be simple to apply but to be honest I expect to not have to use it except for a few edge cases. It's just there if I need it.
My question is when I define position on the diameter I usually come off the dimension, but doesn't this imply it's to the axis. How do I draw it to indicate it is to the surface or does it not matter? Will this impact whether I put a Ø on the tolerance?