EngDesServices
Mechanical
- Feb 13, 2019
- 21
Having the ability to understand and perform hands-on work is something I think helps make engineers better at their job. I re-purposed the old driven gear from my outboard engine as a talking piece about this point and keep it on my desk to remind me that even small design decisions can lead to big problems.
My theory is the failure of a $5 seal, when combined with a not easily inspected location, was what resulted in a total engine failure while 15 miles offshore.
When the seal failed, saltwater was able to make its way into the splines mating the driveshaft of the lower unit to the driven gear. The splines are very shallow and the corrosion of them allowed the shaft to slip, no longer transferring power to the driveshaft, prop-shaft and therefore the propeller.
Replacement of this component required removing the entire powerhead and 8ish hours of labor.
What design ideas do you have for what could have been done to prevent a failure like this?
Michael Hall, PE (TX) PMP - President
Engineering Design Services LLC
My theory is the failure of a $5 seal, when combined with a not easily inspected location, was what resulted in a total engine failure while 15 miles offshore.
When the seal failed, saltwater was able to make its way into the splines mating the driveshaft of the lower unit to the driven gear. The splines are very shallow and the corrosion of them allowed the shaft to slip, no longer transferring power to the driveshaft, prop-shaft and therefore the propeller.
Replacement of this component required removing the entire powerhead and 8ish hours of labor.
What design ideas do you have for what could have been done to prevent a failure like this?
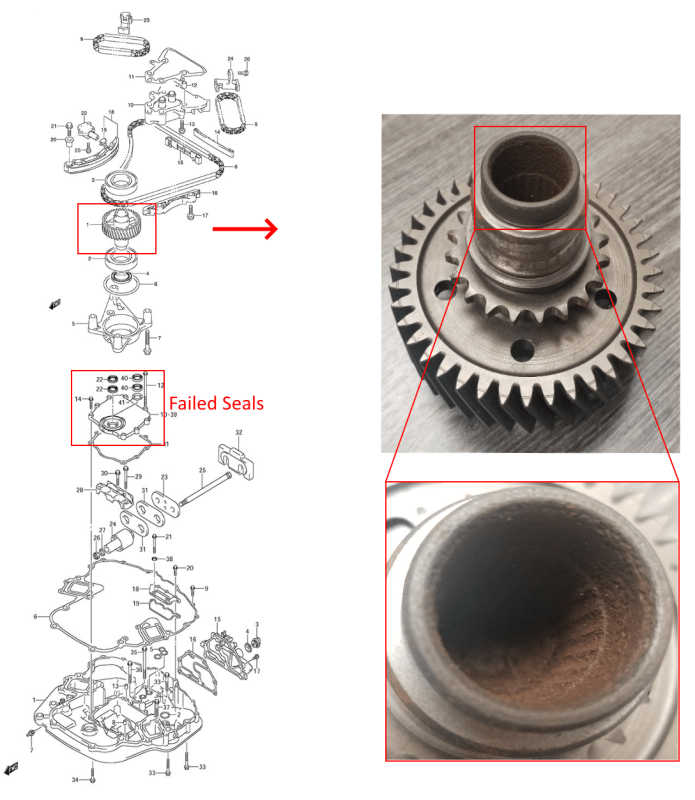
Michael Hall, PE (TX) PMP - President
Engineering Design Services LLC