Burunduk
Mechanical
- May 2, 2019
- 2,580
Considering the tolerance of position for a countersink as shown in this video
Would you interpret the position requirement (when considered for the countersink feature), as applying to the cone axis, or to the center point of the circular element which is controlled for size ø.675-.685?
Would you interpret the position requirement (when considered for the countersink feature), as applying to the cone axis, or to the center point of the circular element which is controlled for size ø.675-.685?
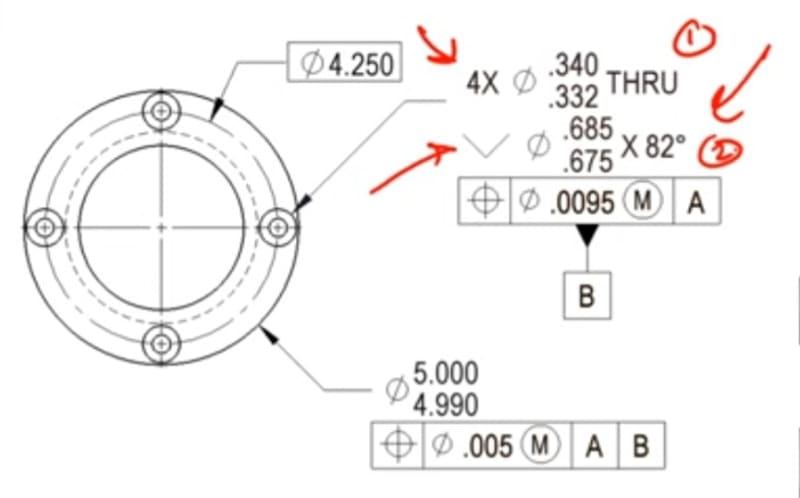