Hi!
I have a case as shown in the picture below. The shaft between the couplings have no support.
The problem is that i get shock loads but not when the engine is running. I have solved the case where i get a axiell shock load by pressing the axis toward each outer hence i get no axial movement of
the coupling (but it would be good to have a coupling who could handle some axial movement)
The case i am wondering about is when i get a radial shock load. I need a couplings with a rated torque of about 800Nm and i get a chock load in shaft 2 of 5kN hence 2,5kN on each coupling. Do you guys have any suggestion on what coupling i could use?
I have a case as shown in the picture below. The shaft between the couplings have no support.
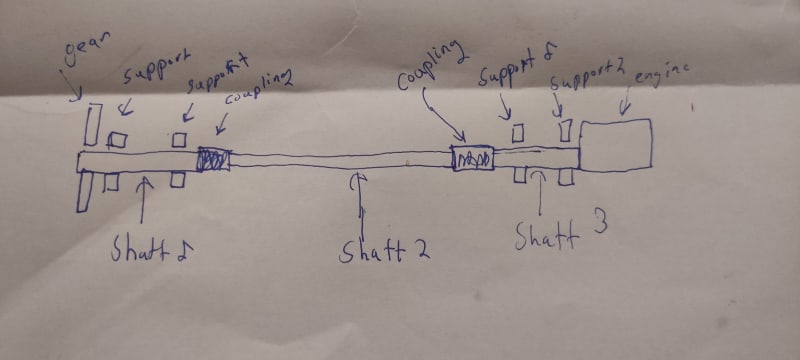
The problem is that i get shock loads but not when the engine is running. I have solved the case where i get a axiell shock load by pressing the axis toward each outer hence i get no axial movement of
the coupling (but it would be good to have a coupling who could handle some axial movement)
The case i am wondering about is when i get a radial shock load. I need a couplings with a rated torque of about 800Nm and i get a chock load in shaft 2 of 5kN hence 2,5kN on each coupling. Do you guys have any suggestion on what coupling i could use?