We have faced heavy rejections in past couple of months in the Roll Milling Rolls that we manufacture(like Work Roll, Idler Roll, Back up roll, leveller roll) for some of the big market players in the world. In all the materials we are facing this issue, no matter how big the Raw Material supplier is. We make purchase AISI D2/D3, SAE52100, AISI H11.
Mainly the cracks are located on the Barrel dia, precisely at the end portions of the barrel length.
HRc: for SAE52100 ranges between 62-66 HRc; for D2 ranges between 61-63 HRc; for H 11 between 58-60HRc.
The Raw material is thoroughly inspected when it comes in Chemistry, UT, Micro and macro testing with 100x,500x zoom microscope. if found in limits they are accepted, otherwise rejected there itself and are not used for further process.
According to my view these are Grinding Cracks, I have to understand what are the different types of grinding cracks and how they are occured. Mainly because the production people apply heavy depth of cut and feed rates on the Hardened roll during the HARD TURNING PROCESS/Grinding Process.
Please help me to understand this. Thanks in advance...
BELOW IS THE LINK OF DRIVE FOR MORE PHOTOGRAPHS:
[]
Mainly the cracks are located on the Barrel dia, precisely at the end portions of the barrel length.
HRc: for SAE52100 ranges between 62-66 HRc; for D2 ranges between 61-63 HRc; for H 11 between 58-60HRc.
The Raw material is thoroughly inspected when it comes in Chemistry, UT, Micro and macro testing with 100x,500x zoom microscope. if found in limits they are accepted, otherwise rejected there itself and are not used for further process.
According to my view these are Grinding Cracks, I have to understand what are the different types of grinding cracks and how they are occured. Mainly because the production people apply heavy depth of cut and feed rates on the Hardened roll during the HARD TURNING PROCESS/Grinding Process.
Please help me to understand this. Thanks in advance...
BELOW IS THE LINK OF DRIVE FOR MORE PHOTOGRAPHS:
[]
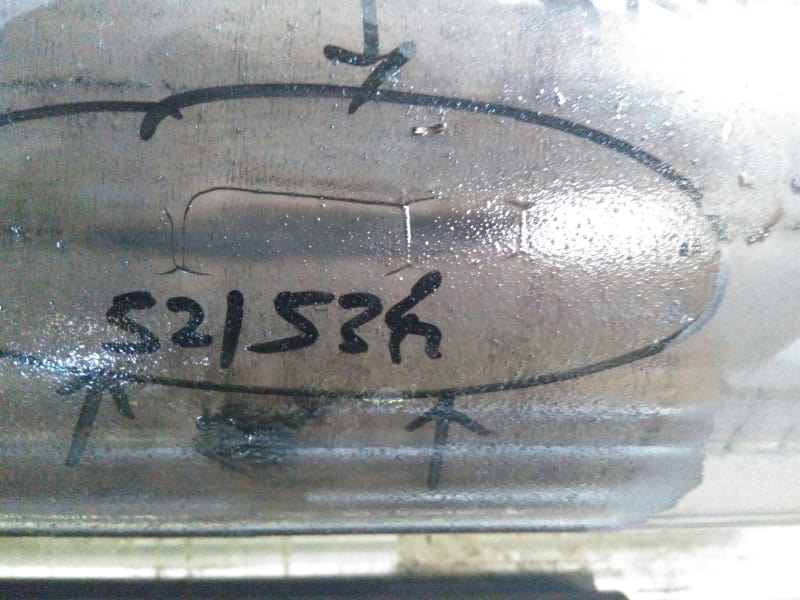