Sriddle
Automotive
- Jul 9, 2024
- 5
Hi all
I am currently designing an aluminum frame for the rear of a truck bed.
The frame will be load bearing and have a dynamic rating of 150kg. I have been asked to perform some 'crash testing' on the frame prototype. This requires a certain amount of force to be exerted on the assembly in a horizontal direction. See example here of a roof rack test performed on a track (
I do not have access to a track or testing facility so was wondering if there is a good way to perform a bench test via pulling on the assembly using a winch or similar device.
What sort of calculations would you recommend to determine the correct load or force? The testing standard ISO11154 states that the load has a force of 8g applied to it and is tested to 1.5 times the stated capacity.
Sorry if this is a tad vague, as you can probably tell I am not a structural engineer, merely a lowly CAD monkey!
Any help would be appreciated.
Steve
I am currently designing an aluminum frame for the rear of a truck bed.
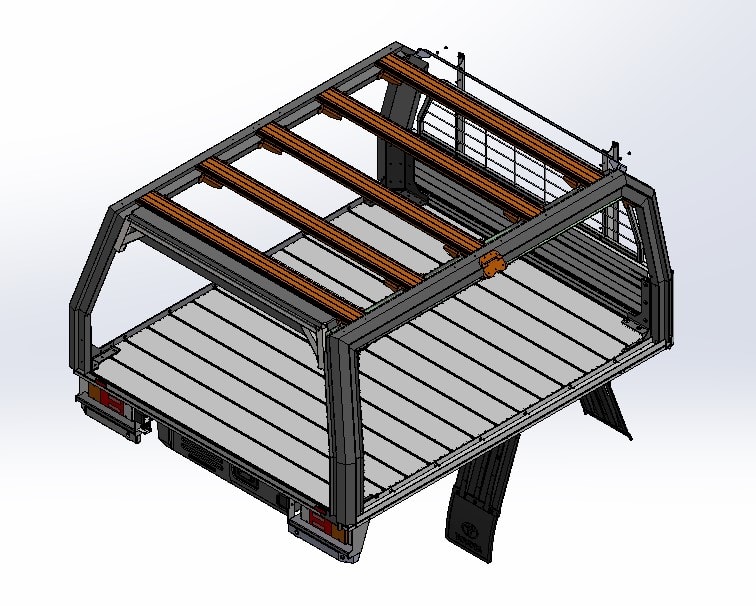
The frame will be load bearing and have a dynamic rating of 150kg. I have been asked to perform some 'crash testing' on the frame prototype. This requires a certain amount of force to be exerted on the assembly in a horizontal direction. See example here of a roof rack test performed on a track (
I do not have access to a track or testing facility so was wondering if there is a good way to perform a bench test via pulling on the assembly using a winch or similar device.
What sort of calculations would you recommend to determine the correct load or force? The testing standard ISO11154 states that the load has a force of 8g applied to it and is tested to 1.5 times the stated capacity.
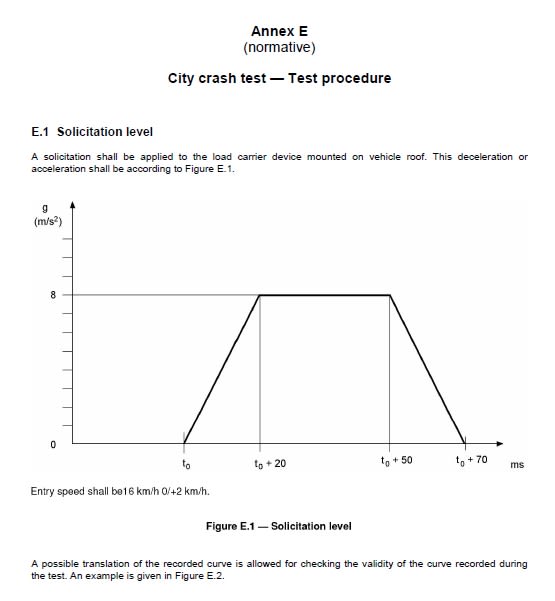
Sorry if this is a tad vague, as you can probably tell I am not a structural engineer, merely a lowly CAD monkey!
Any help would be appreciated.
Steve