Hi All,
Conceptually, I understand, but not sure how to apply to check to see if my part is in spec. Individual measurements are falling out of the range provided, but the averages meet the print.
I have a bushing, on the part the tolerance is given as
70.1 mm
69.9 mm
GD&T is given here
Measurements taken from part
How does this cylindricity of 0.7 relate to the tolerance of 70.1 and 69.9 on the print? Do my values fall within this range?
Thank you.
Conceptually, I understand, but not sure how to apply to check to see if my part is in spec. Individual measurements are falling out of the range provided, but the averages meet the print.
I have a bushing, on the part the tolerance is given as
70.1 mm
69.9 mm
GD&T is given here
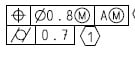
Measurements taken from part

How does this cylindricity of 0.7 relate to the tolerance of 70.1 and 69.9 on the print? Do my values fall within this range?
Thank you.