I have a part that could be described as a "quadruple saddle clamp". Four of these parts will be used to clamp four cylindrical battery cells together (each cell looks like radial electrolytic capacitor, but 18650 sized).
I'm mainly concerned with controlling the positions of the cells relative to each other and making sure they are parallel, so that the leads can be inserted into a mating PCB without excessive stress. Perpendicularity between the cells and the end of the clamp is secondary, and the rest of the profile that is not in contact with the cells does not need to be tightly controlled.
Can anyone recommend an appropriate set of datums for this? I don't use GD&T often, so I'm a bit out of my depth here.
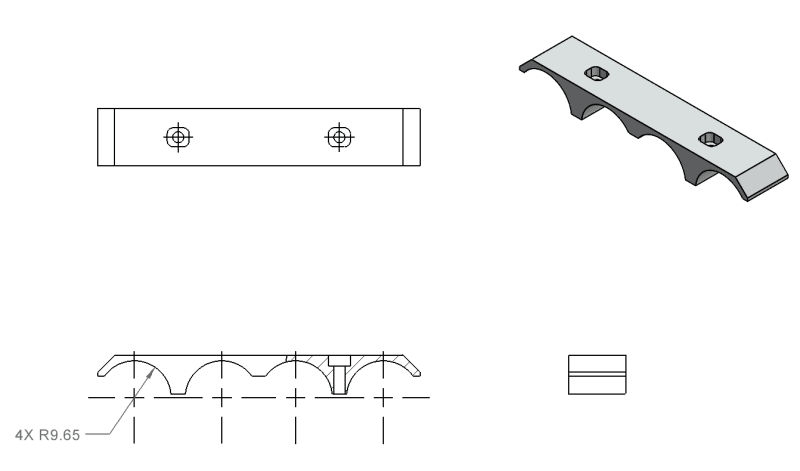
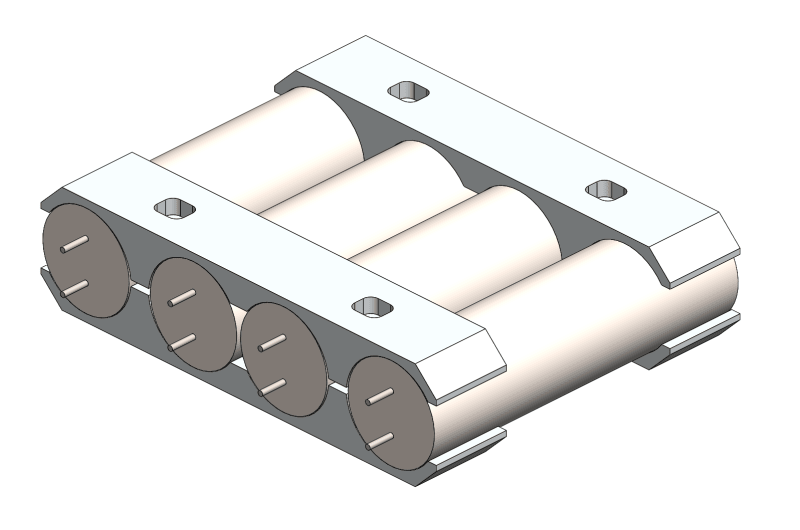
I'm mainly concerned with controlling the positions of the cells relative to each other and making sure they are parallel, so that the leads can be inserted into a mating PCB without excessive stress. Perpendicularity between the cells and the end of the clamp is secondary, and the rest of the profile that is not in contact with the cells does not need to be tightly controlled.
Can anyone recommend an appropriate set of datums for this? I don't use GD&T often, so I'm a bit out of my depth here.