NewbieInSE
Structural
Dear Engineers,
I have attached a figure herewith which will be beneficial in understanding my query.
As you can see, the steel building is three-storied, and some knee braces were added previously to avoid retrofitting of some main steel beams (girders). The purpose was to reduce the length of the member and produce less loads in the girder, which was achieved well.
However, the knee braces' connections are not capable to resist the loads transferred to them in ETABS.
Two bolts can carry about 24.8 kips of shear load.
Whereas in FEM (ETABS) we get a force of about 45 kips due to gravity load combos. Also in some gravity+lateral load combos, the applied load exceeds the capacity of the connection.
Is there any method by which we can declare that these knee braces are provided just to carry say 20 kips forces and the latter forces are not intended for it, equilibrium will be established for the whole structure considering this trade-off (knee braces taking only 20 kips).
Is this justifiable??
This is an existing building, we don't want to apply weld and ignore those bolts to carry the applied loads, because it will be massive work and the factory is in operation.
Thanks....
I have attached a figure herewith which will be beneficial in understanding my query.
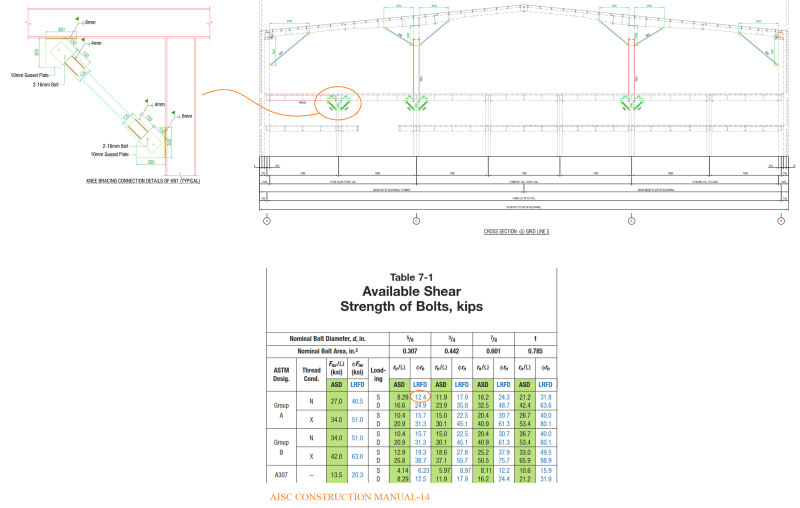
As you can see, the steel building is three-storied, and some knee braces were added previously to avoid retrofitting of some main steel beams (girders). The purpose was to reduce the length of the member and produce less loads in the girder, which was achieved well.
However, the knee braces' connections are not capable to resist the loads transferred to them in ETABS.
Two bolts can carry about 24.8 kips of shear load.
Whereas in FEM (ETABS) we get a force of about 45 kips due to gravity load combos. Also in some gravity+lateral load combos, the applied load exceeds the capacity of the connection.
Is there any method by which we can declare that these knee braces are provided just to carry say 20 kips forces and the latter forces are not intended for it, equilibrium will be established for the whole structure considering this trade-off (knee braces taking only 20 kips).
Is this justifiable??
This is an existing building, we don't want to apply weld and ignore those bolts to carry the applied loads, because it will be massive work and the factory is in operation.
Thanks....