JSD1986
Structural
- May 2, 2012
- 25
Deep Excavation - 13m cut. Approx 8m below water table.
Any quesrions.
Any quesrions.
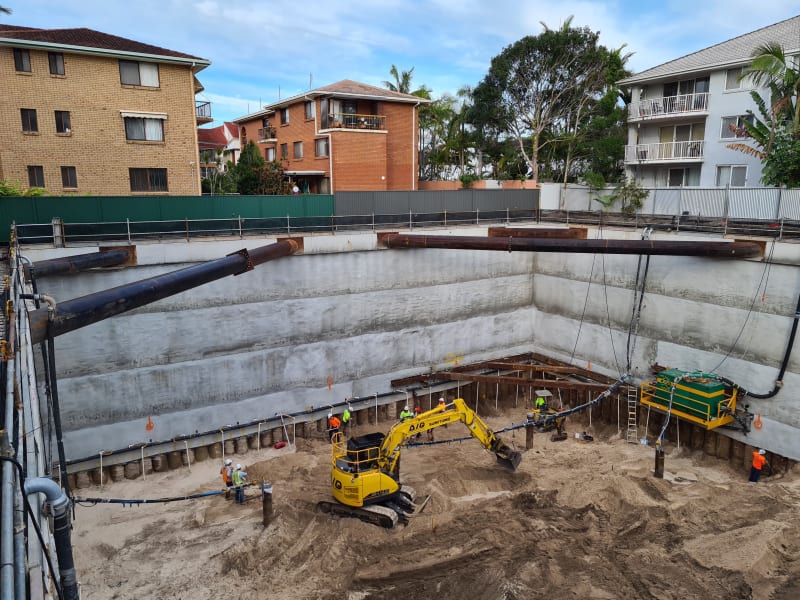
Follow along with the video below to see how to install our site as a web app on your home screen.
Note: This feature may not be available in some browsers.